图书介绍
材料表面工程PDF|Epub|txt|kindle电子书版本网盘下载
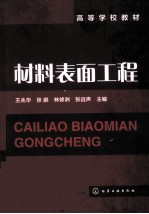
- 王兆华,张鹏,林修洲等主编 著
- 出版社: 北京:化学工业出版社
- ISBN:9787122110299
- 出版时间:2011
- 标注页数:417页
- 文件大小:28MB
- 文件页数:427页
- 主题词:金属表面处理-高等学校-教材
PDF下载
下载说明
材料表面工程PDF格式电子书版下载
下载的文件为RAR压缩包。需要使用解压软件进行解压得到PDF格式图书。建议使用BT下载工具Free Download Manager进行下载,简称FDM(免费,没有广告,支持多平台)。本站资源全部打包为BT种子。所以需要使用专业的BT下载软件进行下载。如BitComet qBittorrent uTorrent等BT下载工具。迅雷目前由于本站不是热门资源。不推荐使用!后期资源热门了。安装了迅雷也可以迅雷进行下载!
(文件页数 要大于 标注页数,上中下等多册电子书除外)
注意:本站所有压缩包均有解压码: 点击下载压缩包解压工具
图书目录
第1章 绪论1
1.1 材料表面基础1
1.1.1 金属的表面1
1.1.2 金属-气体界面3
1.1.3 金属-液体界面4
1.1.4 金属-固体界面4
1.1.5 金属的表面变化5
1.1.6 表面的磨损失效6
1.1.7 表面的疲劳失效7
1.1.8 表面的腐蚀失效8
1.2 材料表面工程概述9
1.2.1 基本概念9
1.2.2 表面工程技术的种类9
1.2.3 常见表面技术方法概述11
1.3 表面工程技术的应用13
1.3.1 表面工程技术在材料科学与工程中的应用13
1.3.2 表面工程技术在腐蚀与防护中的应用14
第2章 表面预处理16
2.1 概述16
2.1.1 预处理的目的16
2.1.2 预处理的重要性17
2.2 机械处理17
2.2.1 磨光17
2.2.2 机械抛光19
2.2.3 刷光21
2.2.4 滚光21
2.2.5 振动磨光21
2.2.6 精加工21
2.2.7 喷砂22
2.3 电解抛光24
2.3.1 电解抛光原理24
2.3.2 工艺规范举例25
2.3.3 工艺操作说明25
2.4 化学抛光26
2.4.1 化学抛光原理27
2.4.2 化学抛光配方27
2.4.3 工艺流程及操作28
2.4.4 化学抛光后处理29
2.5 除油(脱脂)29
2.5.1 有机溶剂除油29
2.5.2 化学除油30
2.5.3 水基清洗剂除油32
2.5.4 电解除油33
2.5.5 滚桶除油33
2.5.6 除油工艺操作34
2.6 浸蚀34
2.6.1 钢铁制品的酸洗35
2.6.2 电化学强浸蚀38
2.7 水洗38
2.7.1 水洗的方法39
2.7.2 水洗操作39
2.8 超声波强化40
2.8.1 超声波清洗原理40
2.8.2 超声波强化除油40
2.8.3 超声波强化浸蚀41
2.9 表面调整41
2.9.1 弱浸蚀41
2.9.2 预浸41
2.9.3 不锈钢的表面调整42
2.9.4 锌合金的表面调整42
2.9.5 铝及铝合金的表面调整43
2.9.6 镁合金的表面调整44
2.9.7 钛及钛合金的表面调整45
2.10 设计预处理工艺流程的几项原则45
第3章 电镀基础47
3.1 绪论47
3.1.1 电镀47
3.1.2 镀层的分类54
3.1.3 镀层选择55
3.2 电镀理论基础61
3.2.1 电极过程61
3.2.2 金属的电结晶65
3.2.3 合金的共沉积69
3.3 镀液性能72
3.3.1 电解液的分散能力72
3.3.2 电解液的覆盖能力77
3.3.3 整平能力79
3.4 镀液质量检验80
3.4.1 Hull槽试验80
3.4.2 电解液的阴极极化性能84
3.4.3 电解液的阳极极化曲线84
3.4.4 阴极电流效率85
3.4.5 电导率85
第4章 电镀工艺87
4.1 单金属镀层87
4.1.1 镀锌87
4.1.2 镀铜94
4.1.3 镀镍98
4.1.4 镀银101
4.1.5 镀铬103
4.2 合金镀层108
4.2.1 镀铜锡合金108
4.2.2 镀铜锌合金109
4.2.3 镀铅锡合金109
4.2.4 碱性锌铁合金电镀111
4.3 特种电镀工艺113
4.3.1 高速电镀113
4.3.2 电刷镀116
4.3.3 复合电镀121
4.3.4 脉冲电镀122
4.3.5 非晶态合金电镀124
4.3.6 熔融盐电沉积126
第5章 电镀工程132
5.1 镀槽132
5.1.1 镀槽的种类132
5.1.2 材质132
5.1.3 尺寸132
5.1.4 设计镀槽时应考虑的其他问题133
5.2 挂具134
5.2.1 挂具的功能134
5.2.2 挂具设计的基本要求134
5.2.3 挂具材料135
5.2.4 挂具结构136
5.2.5 挂具制作137
5.2.6 绝缘处理137
5.2.7 装挂方法138
5.2.8 挂具的使用维护138
5.2.9 提高镀层均匀性的方法138
5.3 镀件绑扎140
5.3.1 绑扎丝140
5.3.2 铜丝的直径140
5.3.3 镀件上绑扎位置141
5.3.4 绑扎一串镀件的长度141
5.3.5 同串镀件之间的距离141
5.3.6 铜丝与镀件绑扎的松紧程度141
5.4 电源142
5.4.1 电镀电源的种类142
5.4.2 电镀电源的选择143
5.4.3 电镀电源的使用144
5.4.4 电镀电源的常见故障分析145
5.4.5 电镀电源的维护与保养145
5.5 输电电路146
5.5.1 交流输入146
5.5.2 直流输出146
5.6 电镀中的阳极147
5.6.1 不溶性阳极147
5.6.2 可溶性阳极147
5.6.3 阳极选择148
5.6.4 合金电镀阳极150
5.7 镀液现场技术151
5.7.1 配制镀液151
5.7.2 镀液净化151
5.7.3 镀液维护155
5.8 电镀辅助设备156
5.8.1 镀液净化设备156
5.8.2 通风设备157
5.8.3 其他设备157
5.9 电镀前准备工作内容157
5.10 退镀158
5.10.1 常用退镀方法158
5.10.2 常见镀层的退镀工艺159
5.11 滚镀160
5.11.1 概述160
5.11.2 滚镀的工艺设备条件161
5.11.3 其他形式的滚镀165
5.11.4 滚镀光亮性锡钴合金工艺规范示例166
5.12 机械镀锌167
5.12.1 概述167
5.12.2 机械镀的沉积机理167
5.12.3 机械镀的工艺设备条件169
5.12.4 机械镀锌的工艺规范示例173
第6章 化学镀175
6.1 概述175
6.1.1 无电源镀层175
6.1.2 化学镀的特点176
6.1.3 化学镀发展简史176
6.1.4 化学镀的类型及应用177
6.2 化学镀镍基础177
6.2.1 化学镀镍层的性质177
6.2.2 化学镀镍的热力学178
6.2.3 化学镀镍的动力学178
6.3 化学镀镍溶液及其影响因素180
6.3.1 主盐180
6.3.2 还原剂180
6.3.3 络合剂181
6.3.4 稳定剂182
6.3.5 加速剂183
6.3.6 缓冲剂184
6.3.7 表面活性剂184
6.4 化学镀镍工艺条件184
6.4.1 基体表面184
6.4.2 镀浴温度185
6.4.3 镀浴pH值186
6.4.4 镀浴化学成分186
6.4.5 搅拌的影响187
6.4.6 镀浴老化及寿命188
6.4.7 化学镀镍液组成和工艺条件示例189
6.5 化学镀镍工艺过程190
6.5.1 镀前准备191
6.5.2 表面预处理192
6.5.3 化学镀镍实务192
6.5.4 镀层质量要求197
6.5.5 影响化学镀镍层性能的因素197
6.6 化学镀铜198
6.6.1 化学镀铜基础199
6.6.2 化学镀铜工艺规范实例201
6.6.3 化学镀铜在塑料电镀中的应用202
第7章 化学转化膜205
7.1 概述205
7.1.1 什么是化学转化膜205
7.1.2 化学转化膜的用途206
7.2 铝及其合金的阳极化206
7.2.1 概述206
7.2.2 铝阳极化的原理207
7.2.3 铝和铝合金的阳极化工艺209
7.2.4 阳极氧化膜的着色与封闭219
7.3 钢铁的化学氧化222
7.3.1 化学氧化膜的性质和用途222
7.3.2 钢铁化学氧化工艺223
7.3.3 钢铁化学氧化的机理224
7.3.4 氧化膜的后处理225
7.3.5 常温发黑工艺225
7.4 钢铁的磷化226
7.4.1 磷化反应226
7.4.2 磷化膜的性质和用途227
7.4.3 转化型磷化228
7.4.4 假转化型磷化228
7.4.5 工业应用233
第8章 热喷涂239
8.1 概述239
8.1.1 什么是热喷涂239
8.1.2 热喷涂技术的分类239
8.1.3 热喷涂技术的特点240
8.2 热喷涂的基础理论241
8.2.1 喷涂层的形成机理241
8.2.2 飞行中的粒子流242
8.2.3 涂层的成分和结构244
8.2.4 涂层的结合机理245
8.3 热喷涂工艺246
8.3.1 喷涂方法246
8.3.2 喷涂材料255
8.3.3 热喷涂工艺256
8.3.4 涂层设计258
第9章 热浸镀260
9.1 绪论260
9.1.1 热浸镀概述260
9.1.2 热浸镀工艺种类260
9.1.3 热浸镀的性能及应用261
9.2 热镀锡262
9.2.1 热镀锡原理262
9.2.2 热镀锡工艺262
9.2.3 热浸镀锡钢板的结构和性能263
9.3 热浸镀锌264
9.3.1 热浸镀锌的性能及应用264
9.3.2 热浸镀锌层原理265
9.3.3 热浸镀锌工艺266
9.3.4 镀锌设备269
9.3.5 影响热镀锌层厚度、结构和性能的因素271
9.3.6 热镀锌涂层检测272
9.3.7 提高热镀锌镀层耐蚀性能的方法273
9.4 热浸镀铝273
9.4.1 热镀铝概述273
9.4.2 热镀铝工艺技术275
9.4.3 热镀铝工艺流程277
9.4.4 热镀铝工艺设备278
第10章 化学热处理279
10.1 概述279
10.1.1 化学热处理概念279
10.1.2 化学热处理的种类279
10.2 扩散镀层形成的机理280
10.2.1 渗层金属的沉积280
10.2.2 渗层原子的扩散281
10.3 渗铝281
10.3.1 渗铝层的形成方法281
10.3.2 渗铝层的组分与结构283
10.3.3 影响渗铝层厚度的因素283
10.3.4 渗铝钢的特性284
10.4 渗铬284
10.4.1 渗铬层的形成方法284
10.4.2 影响渗铬层形成的因素285
10.4.3 渗铬钢材的性能286
10.5 渗硅287
10.5.1 渗硅层的形成方法287
10.5.2 渗硅层的结构和性能288
10.6 渗硼289
10.6.1 渗硼层的形成方法289
10.6.2 渗硼层的组织和性能291
10.7 二元和三元共渗291
10.7.1 铝-铬共渗291
10.7.2 铬-硅共渗292
10.7.3 铬-钛共渗292
10.7.4 铬-硅-铝共渗293
10.8 化学热处理新工艺293
10.8.1 真空渗碳293
10.8.2 离子渗氮295
第11章 耐蚀金属覆盖层298
11.1 堆焊298
11.1.1 金属表面堆焊的特点298
11.1.2 堆焊的应用299
11.1.3 异种金属熔焊基础299
11.1.4 堆焊方法300
11.1.5 堆焊检验306
11.1.6 挤压辊堆焊方法实例306
11.2 钛与钛合金衬里技术307
11.2.1 衬里用纯钛与钛合金307
11.2.2 衬钛309
11.2.3 钛的表面处理309
11.2.4 钛的焊接310
11.2.5 钛衬里的施工方法312
11.2.6 钛衬里的制造要求316
11.3 不锈钢衬里技术318
11.3.1 不锈钢衬里方法318
11.3.2 尿素塔不锈钢衬里319
11.3.3 塞焊法不锈钢衬里321
11.3.4 不锈钢衬里复合管323
11.4 衬铅与搪铅324
11.4.1 铅的性能及其在防腐蚀中的应用324
11.4.2 衬铅的施工技术325
11.4.3 搪铅的施工技术327
第12章 先进表面工程技术331
12.1 材料表面高能束改性处理技术331
12.1.1 概述331
12.1.2 激光束表面改性处理技术332
12.1.3 电子束表面改性处理技术339
12.1.4 离子束表面改性处理技术(离子注入)341
12.2 气相沉积技术347
12.2.1 概述347
12.2.2 物理气相沉积347
12.2.3 化学气相沉积(CVD)357
12.2.4 物理气相沉积与化学气相沉积的对比365
12.3 材料表面复合处理技术366
12.3.1 概述366
12.3.2 热处理与表面形变强化的复合366
12.3.3 镀覆层与热处理的复合366
12.3.4 电镀(镀覆层)与化学热处理的复合367
12.3.5 激光增强电镀和电沉积368
12.3.6 表面热处理与表面化学热处理的复合强化处理368
12.3.7 复合表面化学热处理369
12.3.8 化学热处理与气相沉积的复合369
12.3.9 离子氮碳共渗与离子氧化复合处理技术370
12.3.10 激光淬火与化学热处理的复合370
12.3.11 覆盖层与表面冶金化的复合370
12.3.12 热喷涂与喷丸的复合371
12.3.13 堆焊与激光表面处理的复合371
12.3.14 等离子喷涂与激光技术的复合372
12.3.15 激光束复合气相沉积技术372
12.3.16 电子束复合气相沉积技术373
12.3.17 离子束复合气相沉积技术373
12.4 其他先进表面工程技术374
12.4.1 表面微细加工技术374
12.4.2 纳米表面工程技术381
12.4.3 多弧离子镀技术383
12.4.4 超硬涂层表面技术385
12.4.5 摩擦搅拌表面改性技术385
第13章 材料表面性能测试与控制387
13.1 常规表面性能测试387
13.1.1 外观检查387
13.1.2 厚度测量387
13.1.3 孔隙率389
13.1.4 镀层结合力390
13.1.5 镀层硬度391
13.1.6 镀层脆性391
13.1.7 镀层内应力392
13.1.8 耐蚀性393
13.2 表面分析与测试396
13.2.1 概述396
13.2.2 表面分析与测试的内容396
13.2.3 表面分析技术399
13.3 表面性能的设计控制401
13.3.1 提高材料表面耐磨性的措施401
13.3.2 材料表面的腐蚀控制406
13.3.3 材料高温氧化和疲劳破坏的控制407
13.4 表面处理过程的质量控制409
13.4.1 表面预处理409
13.4.2 表面镀覆过程质量控制412
13.4.3 后处理过程质量控制415
13.4.4 质量过程控制的控制点及因素415
参考文献416