图书介绍
难加工材料磨削技术PDF|Epub|txt|kindle电子书版本网盘下载
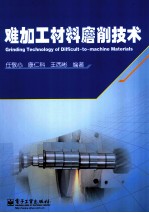
- 任敬心,康仁科,王西彬编著 著
- 出版社: 北京:电子工业出版社
- ISBN:9787121124891
- 出版时间:2011
- 标注页数:388页
- 文件大小:61MB
- 文件页数:402页
- 主题词:难加工材料切削-磨削
PDF下载
下载说明
难加工材料磨削技术PDF格式电子书版下载
下载的文件为RAR压缩包。需要使用解压软件进行解压得到PDF格式图书。建议使用BT下载工具Free Download Manager进行下载,简称FDM(免费,没有广告,支持多平台)。本站资源全部打包为BT种子。所以需要使用专业的BT下载软件进行下载。如BitComet qBittorrent uTorrent等BT下载工具。迅雷目前由于本站不是热门资源。不推荐使用!后期资源热门了。安装了迅雷也可以迅雷进行下载!
(文件页数 要大于 标注页数,上中下等多册电子书除外)
注意:本站所有压缩包均有解压码: 点击下载压缩包解压工具
图书目录
第1章 磨削的基本参数1
1.1 磨削的特点1
1.2 磨削参数4
1.2.1 砂轮与工件的接触长度ls4
1.2.2 砂轮有效磨刃数5
1.2.3 一个磨刃的未变形切屑最大厚度agmax10
1.2.4 当量磨削厚度aeq14
1.2.5 砂轮当量磨削直径de16
第2章 难加工材料的材料特性及磨削加工性的评定17
2.1 常用难加工材料的分类和材料特性17
2.1.1 钛合金17
2.1.2 高温合金20
2.1.3 金属间化合物基高温结构材料23
2.1.4 超高强度钢25
2.1.5 不锈钢27
2.1.6 工程陶瓷29
2.2 难加工材料磨削加工性的评定32
2.2.1 以磨削力评定磨削加工性33
2.2.2 以磨削温度评定磨削加工性37
2.2.3 以磨削表面粗糙度评定磨削加工性42
2.2.4 以磨削表面变质层评定磨削加工性45
2.2.5 以磨削比评定磨削加工性51
第3章 钛合金的磨削56
3.1 钛合金的材料特性及磨削特点56
3.1.1 钛合金的材料特性56
3.1.2 钛合金的磨削特点57
3.2 磨削钛合金的砂轮磨损59
3.2.1 黏附磨损59
3.2.2 磨粒的磨耗与破碎63
3.2.3 扩散磨损67
3.3 磨削钛合金的磨削力69
3.3.1 黏附对磨削力的影响69
3.3.2 黏附条件下的磨削力数学模型70
3.3.3 钛合金磨削力的经验计算式75
3.4 磨削钛合金的磨削温度77
3.4.1 钛合金磨削温度场的理论计算77
3.4.2 钛合金磨削表面温度及磨削温度场的测量82
3.5 钛合金磨削表面完整性86
3.5.1 表面粗糙度86
3.5.2 磨削表层元素变化及气体杂质的污染88
3.5.3 磨削表层的塑性变形88
3.5.4 磨削表层显微硬度的变化90
3.5.5 钛合金磨削烧伤表层的成分变化92
3.5.6 磨削表层残余应力92
3.5.7 疲劳性能95
3.6 磨削钛合金的磨削液97
3.6.1 钛合金对磨削液的要求97
3.6.2 磨削液特性对磨削性能的影响98
3.6.3 磨削钛合金的水溶性磨削液99
3.6.4 磨削钛合金的磨削油102
3.6.5 磨削钛合金的砂轮固体浸渗润滑剂106
3.7 立方氮化硼(CBN)砂轮磨削钛合金108
3.7.1 CBN磨料的性能及CBN砂轮的种类108
3.7.2 陶瓷结合剂CBN砂轮磨削钛合金110
3.8 钛合金的缓进给磨削115
3.8.1 缓进给磨削的特点115
3.8.2 钛合金缓进给磨削的磨削温度和磨削烧伤117
3.8.3 钛合金磨削表层的残余应力121
3.8.4 缓进给磨削中抑制烧伤的措施122
3.9 磨削钛合金的砂轮参数及磨削加工用量的选择127
3.9.1 砂轮的选择原则127
3.9.2 磨削加工用量的选择原则130
3.9.3 磨削加工用量和砂轮参数的选择132
第4章 高温合金的磨削139
4.1 高温合金的材料特性及磨削特点139
4.1.1 高温合金的材料特性139
4.1.2 高温合金的磨削特点141
4.2 高温合金的磨削力和磨削温度142
4.2.1 高温合金的磨削力142
4.2.2 磨削高温合金的磨削温度及磨削温度场146
4.3 磨削高温合金的砂轮磨损151
4.3.1 磨削高温合金时砂轮表面的黏附151
4.3.2 磨削高温合金的磨削比152
4.4 高温合金磨削表面完整性154
4.4.1 高温合金的磨削表面粗糙度155
4.4.2 高温合金磨削后的表层硬度变化158
4.4.3 高温合金的磨削残余应力161
4.4.4 高温合金磨削表层的微观组织变化164
4.4.5 磨削表面完整性对高温合金材料疲劳强度的影响167
4.5 高温合金的缓进给磨削176
4.5.1 高温合金的缓进给磨削烧伤176
4.5.2 缓进给磨削工艺的合理应用181
4.6 磨削高温合金的砂轮参数及磨削加工用量的选择186
4.6.1 砂轮的选择原则186
4.6.2 磨削加工用量的选择原则188
4.6.3 磨削加工用量和砂轮参数的选择188
第5章 超高强度钢的磨削196
5.1 超高强度钢的性能和磨削特点196
5.1.1 超高强度钢的性能196
5.1.2 超高强度钢的磨削特点198
5.2 超高强度钢的磨削力和磨削温度199
5.2.1 超高强度钢的磨削力199
5.2.2 超高强度钢的磨削温度203
5.3 超高强度钢的磨削烧伤及其判别方法205
5.3.1 超高强度钢磨削烧伤表面的形貌205
5.3.2 超高强度钢磨削烧伤表面酸洗后的形貌207
5.3.3 超高强度钢磨削烧伤层的金相分析209
5.3.4 超高强度钢磨削烧伤的巴克豪森噪声检测211
5.4 超高强度钢磨削表面完整性212
5.4.1 超高强度钢磨削表面粗糙度212
5.4.2 超高强度钢磨削表层的显微硬度变化214
5.4.3 超高强度钢磨削表层的残余应力216
5.4.4 超高强度钢磨削表面完整性对疲劳强度的影响221
5.5 超高强度钢低应力无烧伤磨削的措施224
5.6 磨削超高强度钢的砂轮参数及磨削加工用量的选择226
5.6.1 砂轮的选择原则226
5.6.2 磨削加工用量的选择原则227
5.6.3 磨削加工用量和砂轮参数的选择227
第6章 不锈钢的磨削233
6.1 不锈钢的材料特性及磨削特点233
6.1.1 不锈钢的材料特性233
6.1.2 不锈钢的磨削特点234
6.2 磨削不锈钢的砂轮磨损235
6.2.1 砂轮磨损特征235
6.2.2 砂轮磨损率239
6.3 磨削不锈钢的磨削力242
6.3.1 砂轮黏附条件下的磨削力数学模型242
6.3.2 砂轮磨损类型Ⅰ的磨削力245
6.3.3 砂轮磨损类型Ⅱ的磨削力246
6.3.4 砂轮磨损类型Ⅲ的磨削力246
6.4 不锈钢磨削表面完整性249
6.4.1 磨削加工硬化和残余应力249
6.4.2 不锈钢的磨削烧伤250
6.4.3 不锈钢的磨削划伤253
6.5 磨削不锈钢的砂轮参数及磨削加工用量的选择260
6.5.1 砂轮的选择原则260
6.5.2 磨削加工用量的选择原则263
6.5.3 磨削加工用量和砂轮参数的选择264
第7章 典型工程陶瓷的磨削275
7.1 典型工程陶瓷的性能及磨削特点275
7.1.1 典型工程陶瓷的组成与显微结构275
7.1.2 典型工程陶瓷的性能及用途279
7.1.3 典型工程陶瓷的磨削特点282
7.2 典型工程陶瓷的磨削过程及磨削表面微观形貌283
7.2.1 超硬磨料砂轮及其修整283
7.2.2 工程陶瓷磨削的材料去除机理及磨削表面的形成288
7.2.3 典型工程陶瓷磨削表面的微观形貌293
7.3 典型工程陶瓷的磨削力298
7.3.1 工程陶瓷磨削力的理论计算298
7.3.2 陶瓷磨削力的经验计算式302
7.3.3 陶瓷磨削力的频谱分析303
7.3.4 陶瓷磨削力的特点306
7.3.5 影响陶瓷磨削力的因素308
7.4 典型工程陶瓷的磨削温度310
7.4.1 工程陶瓷磨削温度的理论分析311
7.4.2 工程陶瓷磨削温度的测量314
7.4.3 磨削条件对工程陶瓷磨削温度的影响318
7.4.4 工程陶瓷磨削温度的经验计算式320
7.5 典型工程陶瓷磨削工艺参数的选取321
7.5.1 砂轮性能参数321
7.5.2 磨削加工用量325
7.5.3 其他磨削条件的选择330
7.6 典型工程陶瓷的磨削新工艺331
7.6.1 工程陶瓷的高效深切磨削技术331
7.6.2 工程陶瓷的定压力磨削法332
7.6.3 工程陶瓷的镜面磨削法333
7.6.4 工程陶瓷的超声振动磨削技术338
第8章 单晶硅片的磨削342
8.1 单晶硅的材料特性及磨削特点343
8.1.1 单晶硅的材料特性343
8.1.2 单晶硅片的磨削特点345
8.2 单晶硅片的磨削技术346
8.2.1 转台式磨削346
8.2.2 硅片旋转磨削347
8.2.3 双面磨削348
8.3 硅片的超精密磨削机理349
8.3.1 超精密磨削硅片的材料去除机理349
8.3.2 超精密磨削硅片表面的形成机理355
8.4 硅片磨削表面完整性362
8.4.1 磨削试验条件363
8.4.2 磨削硅片的表面微观形貌和损伤363
8.4.3 磨削硅片的亚表面损伤365
8.5 硅片的磨削工艺参数的选择377
8.5.1 工艺试验条件377
8.5.2 工艺参数对磨削过程的影响及其选择378
参考文献381