图书介绍
金属塑性成形手册 下PDF|Epub|txt|kindle电子书版本网盘下载
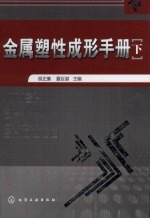
- 胡正寰,夏巨谌主编 著
- 出版社: 北京:化学工业出版社
- ISBN:9787122053206
- 出版时间:2009
- 标注页数:775页
- 文件大小:110MB
- 文件页数:790页
- 主题词:金属压力加工-塑性变形-技术手册
PDF下载
下载说明
金属塑性成形手册 下PDF格式电子书版下载
下载的文件为RAR压缩包。需要使用解压软件进行解压得到PDF格式图书。建议使用BT下载工具Free Download Manager进行下载,简称FDM(免费,没有广告,支持多平台)。本站资源全部打包为BT种子。所以需要使用专业的BT下载软件进行下载。如BitComet qBittorrent uTorrent等BT下载工具。迅雷目前由于本站不是热门资源。不推荐使用!后期资源热门了。安装了迅雷也可以迅雷进行下载!
(文件页数 要大于 标注页数,上中下等多册电子书除外)
注意:本站所有压缩包均有解压码: 点击下载压缩包解压工具
图书目录
第5篇 零件轧制成形1
第1章 辊锻4
1 概述4
2 辊锻变形的基本原理4
2.1 辊锻变形区及其几何参数4
2.2 咬入条件5
2.3 辊锻时金属的延伸5
2.4 辊锻时金属的纵向流动及前滑与后滑6
2.5 辊锻过程中的宽展7
2.6 辊锻力及辊锻力矩9
3 辊锻工艺与模具设计11
3.1 辊锻模结构与材料11
3.2 制坯辊锻工艺12
3.3 成形辊锻工艺18
4 辊锻机20
4.1 辊锻机的工作原理20
4.2 辊锻机的类型20
4.3 辊锻机的技术参数21
4.4 辊锻机的选用23
5 辊锻工艺应用实例23
5.1 连杆辊锻23
5.2 叶片成形辊锻25
5.3 汽车前轴辊锻26
5.4 汽车变截面板簧片精密辊锻28
第2章 楔横轧29
1 概述29
1.1 工作原理29
1.2 工艺特点29
1.3 国内外发展与应用简况29
1.4 工艺流程与车间布置30
2 轧制理论31
2.1 运动原理31
2.2 轧件旋转条件32
2.3 展宽角34
2.4 轧齐理论36
3 变形机理37
3.1 有限元数值模拟37
3.2 轧件上的应变场38
3.3 轧件的变形40
3.4 轧件上的应力场43
3.5 轧件心部缺陷产生机理44
4 轧制压力与力矩48
4.1 模具与轧件接触面积48
4.2 数值计算数据49
4.3 轧制实测数据51
4.4 影响因素综合52
5 模具设计52
5.1 模具设计的一般原则52
5.2 工艺参数的确定54
5.3 对称轴类件的模具设计55
5.4 非对称轴类件的模具设计56
6 机械设备57
6.1 楔横轧机的基本类型57
6.2 楔横轧机的总体配置59
第3章 孔型斜轧61
1 概述61
1.1 工作原理61
1.2 工艺特点61
1.3 国内外发展与应用简况61
1.4 工艺流程与车间布置62
2 轧制原理63
2.1 斜轧回转体运动原理63
2.2 斜轧螺旋体运动原理64
2.3 辊形曲面65
3 变形机理66
3.1 有限元数值模拟66
3.2 轧件上的应变场67
3.3 轧件上的应力场68
3.4 轧件心部疏松机理69
4 轧制压力与力矩71
4.1 轧辊与轧件的接触面积71
4.2 接触面上的单位压力72
4.3 轧制力的方向74
4.4 轧制压力与力矩的实验74
5 模具设计75
5.1 模具设计一般原则75
5.2 孔型参数确定76
5.3 孔型设计方法77
5.4 模具设计实例80
6 机械设备81
6.1 斜轧机的基本类型81
6.2 穿孔式斜轧机82
第4章 环件轧制89
1 环件轧制成形原理90
1.1 环件轧制几何学90
1.2 环件轧制静力学90
1.3 环件轧制运动学92
2 变形主要特征和工艺参数95
2.1 矩形截面环件轧制变形规律95
2.2 环件轧制工艺参数96
3 环件轧制力能参数98
3.1 环件闭式轧制力能计算98
3.2 环件开式轧制力能计算98
3.3 阶梯孔环件闭式轧制力能计算98
3.4 力能计算举例98
3.5 环件轧制力和力矩影响因素99
4 环件轧制工艺与模具设计100
4.1 下料100
4.2 加热100
4.3 环件锻件和毛坯设计101
4.4 环件轧制模具设计和调试104
4.5 环件轧制缺陷和工艺调试106
5 环件轧制设备108
5.1 立式轧环机108
5.2 卧式轧环机109
5.3 精密冷轧环机110
6 环件轧制工艺实例110
6.1 环件轧制生产线110
6.2 典型环件轧制工艺流程110
第5章 摆动辗压112
1 摆辗工艺的特点、分类及应用112
1.1 摆辗成形的原理112
1.2 摆辗工艺的基本特点112
1.3 圆柱形件摆辗变形的基本规律112
1.4 摆辗工艺的分类113
1.5 摆辗工艺的适用范围114
2 摆辗工艺主要的工艺参数114
2.1 摆角γ114
2.2 每转进给量S114
2.3 摆头转速n115
2.4 摆头轨迹115
3 摆辗工艺的力能参数116
3.1 摆辗接触面积率λ116
3.2 摆辗力116
3.3 摆头电动机功率116
4 摆辗工艺的模具设计117
4.1 摆辗模具工况117
4.2 摆辗成形件图的设计117
4.3 摆辗模模具设计117
5 摆动辗压设备120
5.1 摆动辗压设备的工作原理120
5.2 摆动辗压设备的分类120
5.3 摆动辗压设备的主要参数121
5.4 摆动辗压设备的结构121
6 摆辗模具材料123
6.1 热摆辗模具材料123
6.2 冷摆辗模具材料125
7 典型零件的摆辗工艺126
7.1 冷摆辗成形件126
7.2 温、热摆辗成形件128
第6章 径向锻造130
1 径向锻造的工艺原理、用途和优缺点130
1.1 径向锻造的工艺原理130
1.2 径向锻造工艺的用途130
1.3 径向锻造工艺的优缺点130
2 径向锻造设备131
2.1 径向锻造机的分类131
2.2 径向锻造机的构造131
3 径向锻造的力能参数137
3.1 径向锻造机锻造变形力的计算137
3.2 锤头行程、运动速度和加速度138
3.3 径向锻造的变形功139
3.4 径向锻造机电动机功率计算139
4 径向锻造的主要工艺参数139
4.1 径向锻造的主要工艺参数139
4.2 径向锻造的其他工艺参数140
4.3 工艺卡片的编制140
5 径向锻造的锤头、夹爪和芯棒的设计140
5.1 锤头140
5.2 夹爪143
5.3 芯棒143
6 径向锻造工艺的设计及其实例144
6.1 径向锻造工艺的设计144
6.2 坯料146
6.3 变形过程147
6.4 工艺实例147
6.5 径向锻造锻件常见工艺缺陷及其预防措施150
第7章 旋压151
1 概述151
1.1 分类和特点151
1.2 用途155
2 成形原理(变薄旋压)156
2.1 主体运动156
2.2 变形规律156
3 坯料158
3.1 可旋材料158
3.2 普旋坯料158
3.3 剪切旋压坯料159
3.4 流动旋压坯料160
4 工艺参数160
4.1 剪切旋压160
4.2 流动旋压161
5 力能参数162
5.1 力学分析162
5.2 旋压力计算162
6 工艺装备163
6.1 芯模164
6.2 旋轮165
6.3 尾顶166
6.4 靠模166
6.5 加热装置166
6.6 冷却与润滑167
7 旋压机167
7.1 特点167
7.2 结构组成167
7.3 设备类别167
7.4 设备能力170
8 旋压件的质量控制170
8.1 组织结构170
8.2 力学性能170
8.3 尺寸精度170
8.4 缺陷及消除措施171
9 旋压实例172
9.1 φ356mm封头普旋172
9.2 筒形件变薄旋压实例172
9.3 锥形件变薄旋压实例174
参考文献176
第6篇 特种锻造177
第1章 挤压179
1 挤压理论180
1.1 挤压时金属流动180
1.2 挤压时的附加应力181
1.3 挤压时的外摩擦181
1.4 挤压力的计算181
2 挤压工艺189
2.1 冷挤压工艺189
2.2 温挤压工艺193
2.3 热挤压工艺194
3 挤压模具195
3.1 挤压模具的要求及特点195
3.2 挤压模具的典型模具结构196
3.3 挤压模具工作部分设计196
4 挤压实例199
4.1 汽车活塞销冷挤压199
4.2 轴承套圈的温挤压200
第2章 冷镦锻202
1 冷镦工艺202
1.1 冷镦工艺过程和力的计算202
1.2 典型零件冷镦工艺204
2 自动冷镦机模具205
2.1 冷镦模具的分类205
2.2 自动冷镦机模具结构207
2.3 自动冷镦机模膛尺寸208
3 杆状零件冷镦模具设计209
3.1 冲头设计209
3.2 凹模设计211
3.3 切边模具设计216
4 螺母类零件冷镦模具设计217
4.1 镦球模具设计217
4.2 镦六角模具设计218
4.3 冲孔模具设计220
5 通用模具设计221
5.1 切料模具设计221
5.2 滚压工具设计222
第3章 温锻224
1 温锻成形材料及其加热224
1.1 温锻的特点224
1.2 温锻成形材料224
1.3 温锻温度的选择224
1.4 加热方式的选择227
2 温锻的准备228
2.1 毛坯的准备228
2.2 坯料加热、模具预热和坯料润滑228
2.3 温锻变形力的确定229
3 温锻模具的设计与模具材料230
3.1 温锻模具的要求230
3.2 温锻模具结构230
3.3 凸凹模工作部分的设计231
3.4 温锻模具工作部分材料的选择231
3.5 温锻模具的冷却方法232
4 温锻产品质量控制232
4.1 温锻产品的尺寸精度232
4.2 宏观尺寸变化规律232
4.3 温锻产品的实用公差233
4.4 温锻产品的表面粗糙度233
4.5 温锻产品的显微组织变化233
4.6 温锻产品的力学性能233
5 温锻的应用实例235
5.1 碳素结构钢的温锻235
5.2 合金结构钢的温锻235
5.3 轴承钢的温锻236
5.4 不锈钢的温锻237
第4章 超塑性模锻与等温模锻238
1 金属超塑性理论基础238
1.1 金属的塑性、超塑性238
1.2 超塑性变形的力学特征239
1.3 超塑性变形的机理242
1.4 超塑性变形时的组织结构及性能244
2 超塑性模锻245
2.1 超塑性体积成形的特点245
2.2 常用超塑性材料245
2.3 典型件的超塑性模锻工艺248
2.4 超塑性模锻的锻件图设计250
2.5 超塑性模锻的模具结构及材料250
2.6 润滑252
3 等温模锻252
3.1 等温锻造的基本特点和发展动向252
3.2 等温模锻的工艺装备252
3.3 等温模锻对润滑防护剂的特殊要求255
3.4 典型件的等温模锻工艺255
第5章 液态模锻256
1 液态模锻的工艺原理256
1.1 工艺原理256
1.2 液态模锻的工艺流程256
2 液态模锻成形与凝固特点256
3 液态模锻工艺对设备的要求257
3.1 液锻工艺对设备的要求257
3.2 液锻设备的选择依据257
3.3 液锻用成形设备257
3.4 液态模锻辅助设备259
4 液态模锻工艺方法分类260
4.1 直接加压法(直接液态模锻)260
4.2 间接加压法261
4.3 间接挤注法261
5 液态模锻锻件分类与设计要点261
5.1 液锻件分类261
5.2 成形方案与分模位置262
5.3 加工余量与锻件公差262
5.4 脱模斜度264
5.5 圆角半径265
5.6 液锻件的收缩率265
5.7 液锻件图设计265
6 液态模锻模具结构设计266
6.1 液锻模具设计的基本要求266
6.2 液锻模具设计步骤266
6.3 模具结构分类266
6.4 凹模与凹模套设计267
6.5 凸模与挤压头设计269
6.6 型芯与镶块设计270
6.7 卸件装置设计270
6.8 顶件装置设计270
6.9 导向装置设计270
6.10 排气槽与溢料槽设计270
6.11 模板与凸模固定板设计271
6.12 侧分型机构设计271
6.13 模具预热与冷却272
7 液锻模具材料与热处理273
7.1 液锻模具的性能要求273
7.2 液锻模工作零件的常用材料及热处理要求273
7.3 液锻模其他零件材料及热处理要求273
7.4 液锻用模具材料的选用原则273
8 液锻模具技术要求274
9 液态模锻主要工艺因素及控制275
9.1 金属液的质量275
9.2 浇注温度275
9.3 模具预热温度276
9.4 成形压力(比压)276
9.5 保压时间276
10 液锻模具用(润滑剂)涂料276
10.1 液态模锻模具用涂料的作用276
10.2 液态模具用涂料的性能要求276
10.3 液锻模具常用涂料及喷涂工艺276
参考文献278
第7篇 板管特种成形279
第1章 板管的介质成形281
1 薄板件的介质成形281
1.1 薄板件的弹性介质成形工艺281
1.2 薄板件的液体介质成形工艺283
2 管件的介质成形288
2.1 管件的弹性介质成形工艺288
2.2 管件的液体介质成形工艺及工装设计293
第2章 板料无模成形300
1 多点成形技术基础301
1.1 基本原理301
1.2 基本成形方式301
1.3 成形缺陷的产生与控制302
2 多点成形工艺305
2.1 一次成形306
2.2 分段成形306
2.3 多道次成形307
2.4 反复成形308
2.5 闭环成形309
2.6 薄板多点成形309
3 多点成形设备309
3.1 基本体单元及调形310
3.2 多点成形主机311
3.3 CAD/CAM软件311
3.4 设备规格与应用314
4 增量成形技术315
4.1 基本原理315
4.2 成形分析与实验316
4.3 成形设备317
第3章 旋压成形320
1 普通旋压320
1.1 普通旋压的应用320
1.2 普通旋压的工艺参数320
1.3 普通旋压工装设计325
1.4 旋压力的计算327
1.5 特殊旋压方式328
2 变薄旋压329
2.1 变薄旋压的应用329
2.2 变薄旋压的工艺参数331
2.3 变薄旋压的工装设计335
2.4 变形力336
2.5 特殊旋压方式337
第4章 超塑成形344
1 超塑性成形技术基础344
1.1 定义、特征及特点344
1.2 超塑性机理及变形的影响因素345
1.3 超塑性金属和合金347
2 薄板的超塑性成形工艺348
2.1 超塑性成形方法348
2.2 超塑性成形的工艺参数350
2.3 超塑性成形的结构工艺性352
2.4 零件壁厚不均匀的控制方法353
2.5 超塑性成形工艺过程354
3 超塑性成形模具355
3.1 模具材料355
3.2 模具设计355
4 超塑性成形设备357
4.1 基本要求357
4.2 基本组成357
4.3 国外超塑性成形设备357
5 超塑成形/扩散连接技术358
5.1 钣金的扩散连接358
5.2 组合工艺(SPF/DB)的工艺方法与典型结构361
5.3 超塑成形/扩散连接工艺的应用362
第5章 爆炸成形366
1 工艺参数选择366
1.1 炸药种类366
1.2 药包形状366
1.3 药位367
1.4 药量367
1.5 传压介质368
1.6 水深368
2 爆炸成形装置与模具设计368
2.1 传压介质的盛装装置368
2.2 爆炸成形用模具368
3 工艺分析与实例370
3.1 爆炸拉深370
3.2 爆炸胀形375
3.3 其他形式的爆炸成形377
4 爆炸成形安全守则380
第6章 电磁成形381
1 工艺基础381
1.1 基本原理381
1.2 电磁成形材料381
1.3 电磁成形的坯料383
1.4 线圈383
1.5 集磁器385
1.6 模具及驱动片385
2 连接工艺386
2.1 连接方式386
2.2 管-杆连接的影响因素387
2.3 管-管连接的影响因素388
2.4 连接方式及应用388
3 管坯成形389
3.1 管坯的变形389
3.2 胀径成形390
3.3 缩径成形393
3.4 管状坯料的分离工序396
4 板坯成形396
4.1 平板坯料成形397
4.2 冲裁400
4.3 框架零件成形实例401
5 电磁成形设备402
5.1 设备组成及分类402
5.2 国内外的电磁成形设备403
参考文献405
第8篇 型材挤压成形407
第1章 铝合金型材409
1 铝合金型材的分类409
1.1 分类原则409
1.2 分类方法409
2 铝合金型材断面的设计方法415
2.1 断面形状的复杂性415
2.2 挤压系数416
2.3 断面大小416
2.4 型材壁厚416
2.5 包围空间面积的设计416
2.6 直角间的圆角半径417
2.7 断面尺寸公差417
3 挤压型材常用铝合金及特性417
3.1 常用铝合金化学成分417
3.2 常用铝合金分类418
3.3 常用铝合金及其特性418
4 变形铝合金的挤压性能420
第2章 铝合金型材挤压工艺基础及成形过程数值模拟422
1 铝合金型材挤压时的金属变形规律422
1.1 正挤压时金属变形的基本阶段422
1.2 正挤压实心件的金属流动情况422
1.3 正挤压空心件的金属流动情况422
2 影响型材挤压变形的主要因素分析423
2.1 接触摩擦与润滑423
2.2 凹模角度及形状423
2.3 模孔的排列423
2.4 表面状态424
2.5 加热温度424
2.6 合金性能424
3 型材挤压力的计算424
3.1 别尔林公式424
3.2 古布金公式425
3.3 经验公式425
4 铝合金型材挤压过程有限元数值模拟425
4.1 塑性成形有限元基本理论425
4.2 三维有限元模拟中关键技术的处理425
4.3 铝合金型材非等温挤压过程模拟实例426
4.4 工艺参数对铝型材挤压变形规律的影响429
5 型材挤压过程工艺参数优化模型432
5.1 集数值仿真、人工神经网络和遗传算法为一体的参数优化模型433
5.2 非对称角铝型材挤压成形工艺参数优化实例433
5.3 非对称角铝型材挤压成形过程的数值仿真434
第3章 铝合金型材挤压工艺436
1 挤压坯料的选择436
2 挤压温度与速度的确定436
2.1 挤压温度范围的确定436
2.2 挤压时的速度条件437
3 挤压方法的选择438
3.1 等截面实心型材的挤压方法438
3.2 等截面空心型材的挤压方法438
3.3 阶段变断面实心型材的挤压方法439
3.4 浙变断面实心型材的挤压方法440
4 润滑剂的选用440
5 铝合金型材的生产工艺流程441
第4章 铝合金型材挤压模具设计442
1 铝型材挤压工模具的工作条件442
2 型材挤压模具的分类及组装方式443
2.1 型材挤压模具的分类443
2.2 型材挤压模具的组装方式443
3 型材模具的典型结构参数及外形标准化444
3.1 挤压模结构参数的设计445
3.2 模具的外形尺寸及其标准化445
4 型材挤压模具的设计方法及技术要求446
4.1 模具设计方法446
4.2 模具设计的技术要求447
5 模具结构设计447
5.1 实心型材挤压模具设计447
5.2 空心型材挤压模具设计449
5.3 空心型材平面分流组合挤压模设计452
5.4 阶段变断面型材挤压模设计456
5.5 渐变断面型材挤压模设计458
5.6 扁宽带筋壁板型材挤压模设计460
5.7 民用建筑型材挤压模设计462
第5章 型材挤压凹模优化设计466
1 基于传统方法的优化设计466
1.1 改变模孔工作带的几何形状与尺寸466
1.2 阻碍角的辅助作用468
1.3 采用促流角来均衡金属流速469
1.4 使型材各部分流动速度均匀的其他方法470
2 现代优化设计方法中的两个关键问题470
2.1 目标参数的确定470
2.2 约束条件的确定470
3 型材挤压模工作带长度设计计算的数学建模470
3.1 型材挤压时金属流动规律研究471
3.2 挤压模工作带长度设计计算的数学建模471
3.3 实验验证472
4 U形铝型材挤压模具结构工艺参数优化设计472
4.1 U形型材挤压模具结构优化设计数学模型的建立472
4.2 U形型材挤压过程的有限元模拟472
4.3 神经网络模型的建立与训练473
4.4 采用RPGA为优化算法的优化步骤474
4.5 优化结果的有限元仿真474
5 三维铝型材挤压模多参数优化475
5.1 人工神经网络建模476
5.2 遗传算法优化477
第6章 镁合金型材挤压成形工艺478
1 镁合金的性能特点478
2 镁合金锻造与挤压工艺特点478
2.1 坯料准备478
2.2 锻造与挤压前加热478
2.3 锻造与挤压479
2.4 清理和热处理480
3 镁合金型材挤压成形工艺480
3.1 实验材料及设备480
3.2 挤压工艺参数确定480
3.3 实验研究结果与应用481
参考文献482
第9篇 塑性成形CAD/CAM483
第1章 概论485
1 CAD/CAM的基本概念485
1.1 概念485
1.2 计算机在设计和制造中的辅助作用485
1.3 CAD与CAM的集成486
2 模具CAD/CAM技术的应用486
2.1 CAD/CAM技术在模具行业的应用状况486
2.2 模具CAD/CAM的优越性487
2.3 模具CAD/CAM的特点487
3 传统的模具设计制造与模具CAD/CAM的比较488
3.1 传统的模具设计与制造488
3.2 集成的模具设计制造过程488
4 建立CAD/CAM系统的过程与方法488
第2章 模具CAD/CAM系统的组成491
1 模具CAD/CAM系统的硬件491
1.1 主机491
1.2 外部存储器491
1.3 输入设备492
1.4 输出设备492
2 计算机网络494
3 模具CAD/CAM系统的软件495
3.1 系统软件495
3.2 支撑软件495
3.3 应用软件497
第3章 数据处理方法498
1 常见的数据结构498
1.1 数据结构分类498
1.2 常用数据结构的分析499
2 数表的处理方法500
2.1 以数组的形式存放数表501
2.2 以数据文件形式存放数表501
2.3 函数插值方法502
2.4 交互处理方法502
3 线图的程序化503
4 建立经验公式的方法503
4.1 处理数表的回归分析方法503
4.2 多项式拟合504
4.3 线性拟合与可化为线性拟合的问题504
第4章 CAD/CAM的图形学基础505
1 图形的变换505
1.1 二维图形的变换505
1.2 三维图形的变换506
1.3 透视变换508
2 交互技术509
2.1 交互输入技术509
2.2 用户界面设计510
第5章 CAD/CAM中的几何建模技术512
1 几何造型的基本概念512
1.1 概念512
1.2 几何造型的方法512
2 形体的表示模式513
2.1 体素调用表示513
2.2 空间点列表示513
2.3 单元分解表示513
2.4 扫描变换表示514
2.5 构造体素表示(CSG)514
2.6 边界表示(B-Reps)514
2.7 混合模式515
3 参数化特征建模515
3.1 特征建模技术515
3.2 参数化技术518
3.3 参数化特征造型的基本方法520
4 装配建模技术520
4.1 装配建模的基本概念520
4.2 装配建模的一般方法522
4.3 基于功能组件的模具装配设计方法522
5 曲线与曲面523
5.1 曲线523
5.2 曲面528
第6章 产品数据管理技术531
1 产品数据管理技术概述531
1.1 PDM技术的产生531
1.2 PDM的定义531
1.3 PDM系统的体系结构531
2 PDM系统的功能531
2.1 数据与文档管理532
2.2 过程与工作流程管理532
2.3 产品结构与配置管理533
2.4 零部件分类库管理533
2.5 项目管理533
2.6 其他功能533
3 PDM系统的实施533
3.1 PDM实施的内容533
3.2 PDM实施的基本步骤534
3.3 PDM的信息建模534
3.4 成功实施PDM应注意的几个问题535
4 基于PDM的系统集成536
4.1 基于PDM实现应用集成的三个层次536
4.2 模具CAD/CAPP/CAM与PDM的集成536
第7章 优化设计方法538
1 概论538
1.1 设计变量538
1.2 目标函数538
1.3 约束条件538
1.4 优化设计的数学模型539
2 常用优化设计方法540
3 多维无约束优化方法541
3.1 多维无约束优化问题的直接解法541
3.2 多维无约束优化问题的间接解法543
4 有约束优化方法545
4.1 有约束优化问题的直接解法545
4.2 有约束优化问题的间接解法547
5 组合挤压凹模的优化设计549
5.1 组合凹模的类型和受力特点549
5.2 组合凹模的有限元优化方法550
6 预成形模具形状的优化设计551
6.1 刚(黏)塑性有限元基本方程552
6.2 设计变量与目标函数552
6.3 灵敏度分析553
6.4 预成形模具的优化设计过程553
6.5 少无鼓形圆柱体镦粗过程优化实例554
第8章 数控加工编程技术556
1 概述556
1.1 数控加工的基本概念556
1.2 数控机床的组成、分类及发展558
2 数控加工程序的编制内容与过程559
2.1 数控加工程序编制的内容559
2.2 数控加工程序的编制过程560
3 数控自动编程技术的发展561
4 数控编程中的工艺处理562
4.1 工序、工步的划分和顺序安排562
4.2 零件装夹方法的确定与夹具选择562
4.3 对刀点和换刀点的确定562
4.4 进给路径的规划563
4.5 刀具选择564
4.6 切削用量的确定565
4.7 程编误差及其控制565
5 数控加工程序的编制方法566
5.1 零件编程的通用标准566
5.2 点位、直线控制系统的程序编制570
5.3 轮廓控制系统的程序编制570
6 APT语言572
6.1 几何定义语句572
6.2 刀具运动语句573
6.3 后置处理程序语句575
6.4 辅助语句576
6.5 APT语言应用实例576
7 数控线切割加工程序的编制577
7.1 数控线切割编程中的工艺处理577
7.2 数控线切割加工的程序编制579
8 冲裁模线切割的自动编程580
8.1 生成金属丝运动轨迹580
8.2 穿丝孔和起割点的自动选取580
8.3 自动编程过程581
9 Mastercam软件581
9.1 系统特点概述581
9.2 系统的运行环境和流程582
9.3 系统界面及功能582
9.4 用Mastercam编制NC加工程序的示例583
9.5 注塑模具CAM示例585
第9章 冲压模具CAD587
1 冲裁模系统的结构与功能587
1.1 冲裁模CAD/CAM系统的结构587
1.2 系统的功能与流程587
2 冲裁件工艺性判断588
2.1 判别模型的建立588
2.2 处理图形的几种算法589
2.3 工艺性的自动判别过程589
3 毛坯优化排样590
3.1 毛坯排样问题的数学描述590
3.2 多边形法590
3.3 高度函数法591
3.4 平行线分割纵横平移法592
4 冲裁工艺方案的设计594
4.1 模具类型的选择594
4.2 连续模的工步设计595
5 冲裁模结构设计596
5.1 冲裁模结构设计子系统的功能结构596
5.2 总装图设计596
5.3 凹模和凸模设计597
5.4 顶杆的优化布置598
6 级进模CAD的内容与系统结构600
6.1 级进模的设计内容与过程600
6.2 级进模CAD系统的结构600
6.3 系统的功能模块601
7 基于特征的连续冲压工艺设计601
7.1 钣金零件的单元特征模型601
7.2 基于特征的冲压工艺设计方法603
8 级进模结构与零件CAD604
8.1 级进模结构的装配模型604
8.2 总体结构及零件设计605
9 覆盖件模具CAD系统的结构606
9.1 冲压工艺设计606
9.2 模具结构设计606
10 覆盖件冲压工艺CAPP607
10.1 冲压工艺CAPP系统的总体结构607
10.2 覆盖件冲压工艺的数据库管理系统607
10.3 基于成组技术的检索式工艺设计609
10.4 基于特征的冲压工序详细设计610
11 覆盖件模具结构设计613
11.1 基于典型结构的覆盖件模具结构二维设计613
11.2 基于特征的覆盖件模具结构三维设计614
第10章 注射模CAD615
1 注射模CAD/CAE/CAM概述615
1.1 注射模CAD/CAE/CAM的发展615
1.2 注射模CAD/CAM系统的工作流程615
2 注射模CAD的内容及特点616
2.1 注射模CAD的内容616
2.2 注射模CAD的特点617
2.3 注射模CAD系统的结构617
3 注射模总体结构的设计618
3.1 柔性化的模具总体结构设计618
3.2 基于知识的模具总体结构设计618
4 标准模架选用及编码619
5 镶拼式模具结构设计620
6 成型零部件设计621
6.1 成型零部件尺寸计算621
6.2 分型面的确定621
6.3 成型腔壁厚计算622
6.4 凸、凹模模型的生成622
7 流道系统的设计623
7.1 流道系统的结构623
7.2 流道系统的设计计算624
8 冷却系统设计626
9 注射流动模拟626
9.1 一维流动模拟627
9.2 二维流动模拟628
9.3 三维流动模拟628
10 冷却过程分析629
10.1 冷却分析的数学模型630
10.2 一维冷却分析630
10.3 二维冷却分析630
10.4 三维冷却分析631
第11章 锻模CAD632
1 利用成组技术建立锻模CAD系统的方法632
2 锻件与毛坯形状复杂性的定量计算634
3 锻件毛坯形状优化设计方法634
3.1 目标函数与优化方法634
3.2 优化设计实例636
4 锻造载荷和应力的计算638
4.1 轴对称横向流动638
4.2 轴对称轴向流动639
4.3 平面应变、横向流动639
4.4 平面应变、纵向流动形成筋640
5 轴对称件锻模CAD系统641
5.1 轴对称件锻模CAD/CAM系统的组成641
5.2 轴对称锻件几何形状的输入641
5.3 锻件设计641
5.4 锻模设计642
6 长杆类锻模CAD系统642
6.1 长杆类锻模CAD/CAM系统的总体结构642
6.2 模锻工艺设计642
6.3 拔长型槽的设计643
6.4 滚挤型槽的设计645
6.5 型槽的布置646
7 飞边槽尺寸和飞边金属消耗的计算646
7.1 飞边槽桥部尺寸的算法646
7.2 飞边金属消耗的算法647
8 预锻型槽的设计647
8.1 预锻型槽的设计规则647
8.2 预锻型槽截面的设计方法648
第12章 CAD/CAM的新发展650
1 计算机辅助技术的集成650
1.1 产品建模技术650
1.2 CAD/CAM系统中的产品数据交换650
1.3 CAD/CAM的集成方法652
2 协同设计653
2.1 协同设计的概念653
2.2 协同设计的关键技术653
2.3 系统的结构与管理654
2.4 模具协同设计系统655
3 并行工程656
3.1 并行工程的发展背景656
3.2 并行工程的概念657
3.3 并行工程的支持系统657
3.4 并行工程的过程建模659
3.5 并行开发过程的分析660
3.6 并行工程的组织管理661
3.7 模具制造并行工程662
4 虚拟制造663
4.1 虚拟制造的定义663
4.2 虚拟制造的分类664
4.3 虚拟现实及其实现664
4.4 虚拟制造的体系结构665
4.5 虚拟制造中的关键技术666
4.6 虚拟制造的应用667
参考文献668
第10篇 塑性成形质量控制与检测671
第1章 影响塑性成形件质量的几个主要问题673
1 晶粒度673
1.1 晶粒大小对性能的影响673
1.2 影响晶粒大小的一些主要因素674
1.3 细化晶粒的途径677
2 过热、过烧677
2.1 析出相引起的稳定过热678
2.2 晶粒遗传引起的稳定过热679
2.3 过热对力学性能的影响681
3 金属纤维组织(流线)681
3.1 纤维组织对性能的影响681
3.2 流线分布的原则和实例683
3.3 关于流线的控制683
4 脱碳684
4.1 脱碳对钢性能的影响685
4.2 影响钢脱碳的因素685
4.3 防止脱碳的措施686
5 白点686
5.1 白点对钢的力学性能的影响686
5.2 关于白点形成的原因687
5.3 防止白点产生的措施687
6 折叠688
7 裂纹691
7.1 形成裂纹的力学分析692
7.2 形成裂纹的组织分析693
7.3 锻造裂纹的鉴别与防止产生裂纹的原则措施694
8 空腔694
9 压缩失稳695
第2章 各类金属材料塑性成形件的常见缺陷与控制措施697
1 莱氏体高合金工具钢塑性成形件的常见缺陷与控制措施697
2 不锈耐酸钢塑性成形件的常见缺陷与控制措施702
2.1 铁素体不锈钢702
2.2 奥氏体(包括奥氏体-铁素体)不锈钢704
2.3 马氏体(包括马氏体-铁素体)不锈钢706
3 高温合金塑性成形件的常见缺陷与控制措施707
4 铝合金塑性成形件的常见缺陷与控制措施710
5 镁合金塑性成形件的常见缺陷与控制措施715
6 铜合金塑性成形件的常见缺陷与控制措施719
7 钛合金塑性成形件的常见缺陷与控制措施723
第3章 各主要塑性成形工序中的常见缺陷与控制措施732
1 镦粗过程中的常见缺陷与控制措施732
2 拔长过程中的常见缺陷与控制措施733
2.1 矩形截面坯料的拔长733
2.2 圆截面坯料的拔长735
2.3 空心件拔长736
3 冲孔过程中的常见缺陷与控制措施736
4 扩孔过程中的常见缺陷与控制措施737
5 模锻过程中的常见缺陷与控制措施738
6 挤压过程中的常见缺陷与控制措施740
7 摆动辗压过程中的常见缺陷与控制措施742
8 楔横轧过程中的常见缺陷与控制措施745
9 冲压成形中的常见缺陷与控制措施746
9.1 裂纹746
9.2 起皱747
第4章 大型锻件的常见缺陷与控制措施749
1 大型锻件的常见缺陷及其防治措施749
2 大型锻件生产过程的质量控制753
3 大型锻件质量分析与控制举例754
3.1 转子类锻件的质量分析与控制754
3.2 护环锻件的质量分析与控制756
3.3 叶轮白点的防治757
第5章 锻件质量检验的内容和方法759
1 锻件质量检验的内容759
2 锻件质量检验的方法761
3 探查锻件内部裂纹的两种无损检测方法762
3.1 射线探伤法762
3.2 超声波探伤法762
3.3 射线探伤法和超声波探伤法比较763
4 探查锻件表面缺陷的三种无损检测方法764
4.1 磁粉探伤法764
4.2 液体渗透探伤法764
4.3 涡流探伤法765
4.4 磁粉探伤法、液体渗透探伤法和涡流探伤法的比较765
第6章 锻件生产过程的质量控制766
1 锻件生产准备阶段的质量控制766
1.1 锻件图的质量控制766
1.2 锻造工艺规程的质量控制767
1.3 锻造工装模具图的质量控制767
1.4 锻模制造的质量控制768
2 锻造原材料的质量控制768
2.1 原材料的主要缺陷及其引起的锻件缺陷768
2.2 锻造原材料订货时的要求769
2.3 原材料入厂复验769
2.4 原材料的标记方法769
3 备料过程中的质量控制770
3.1 备料不当产生的缺陷及其对锻件的影响770
3.2 下料工序的质量控制770
4 加热过程中的质量控制771
4.1 加热工艺不当常产生的缺陷771
4.2 加热炉应保持良好的工作状态771
4.3 加热工序的质量控制772
5 锻造工序的质量控制772
5.1 锻造工艺不当常产生的缺陷772
5.2 锻造工序的质量控制773
6 锻件热处理过程的质量控制773
7 锻件清理过程的质量控制774
参考文献775