图书介绍
中国材料工程大典 第16卷 材料表面工程 上PDF|Epub|txt|kindle电子书版本网盘下载
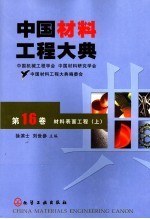
- 徐滨士,刘世参主编;中国机械工程学会,中国材料研究学会,中国材料工程大典编委会编 著
- 出版社: 北京:化学工业出版社
- ISBN:7502573186
- 出版时间:2006
- 标注页数:659页
- 文件大小:91MB
- 文件页数:675页
- 主题词:材料科学;金属表面处理
PDF下载
下载说明
中国材料工程大典 第16卷 材料表面工程 上PDF格式电子书版下载
下载的文件为RAR压缩包。需要使用解压软件进行解压得到PDF格式图书。建议使用BT下载工具Free Download Manager进行下载,简称FDM(免费,没有广告,支持多平台)。本站资源全部打包为BT种子。所以需要使用专业的BT下载软件进行下载。如BitComet qBittorrent uTorrent等BT下载工具。迅雷目前由于本站不是热门资源。不推荐使用!后期资源热门了。安装了迅雷也可以迅雷进行下载!
(文件页数 要大于 标注页数,上中下等多册电子书除外)
注意:本站所有压缩包均有解压码: 点击下载压缩包解压工具
图书目录
第1篇 概论1
2 表面工程的功能3
1 表面工程3
第1章 表面工程的内涵及功能3
3 表面涂覆5
2 表面处理5
第2章 表面工程技术的分类5
1 表面改性5
5 纳米表面工程技术6
4 复合表面工程技术6
2 表面工程发展的三个阶段7
1 表面工程概念的提出7
第3章 表面工程的发展7
2 发展表面工程是贯彻可持续发展战略建设节能型社会和保护环境的需要8
1 发展表面工程是提升机电产品服役性能、支持制造业技术创新的需要8
第4章 发展表面工程的意义8
3 发展表面工程是大力推进废旧机电产品再制造的需要9
5 发展表面工程是提高人民生活水平的需要10
4 发展表面工程是促进电子电器高新技术和生物医学材料发展的需要10
参考文献11
第2篇 材料服役中表面的失效行为及防治13
1.1 热力学概念15
1 腐蚀破坏理论基础15
第1章 腐蚀失效15
1.2 动力学概念18
1.3 高温腐蚀22
1.4 非金属腐蚀25
2.2 孔蚀28
2.1 全面(均匀)腐蚀28
2 腐蚀失效类型28
2.4 晶间腐蚀29
2.3 缝隙腐蚀29
2.5 选择性腐蚀30
2.6 应力腐蚀破裂31
3.1 选材和设计32
3 腐蚀失效的防治32
2.7 氢损伤:氢腐蚀、氢鼓泡、氢脆32
3.3 加入缓蚀剂(无机缓蚀剂、有机缓蚀剂、气相缓蚀剂)33
3.2 改善环境33
3.4 阴极保护35
3.6 合金化36
3.5 阳极保护36
3.7 表面处理37
3.8 金属镀层和包覆层39
3.10 衬里40
3.9 涂层40
1.1 固体表面42
1 磨损破坏的理论基础42
第2章 磨损失效42
1.2 固体表面接触机制44
1.3 摩擦学模型46
1.4 磨损理论49
2.1 磨料磨损52
2 磨损失效的类型52
2.2 黏着磨损55
2.3 疲劳磨损57
2.4 冲蚀磨损58
2.5 腐蚀磨损60
2.6 微动磨损61
3.1 磨料磨损的控制62
3 磨损失效的防治62
3.3 疲劳磨损的控制64
3.2 黏着磨损的控制64
3.4 冲蚀磨损的控制65
3.6 微动磨损的控制66
3.5 腐蚀磨损的控制66
3.7 纳米涂层防磨技术简介67
1.1 高循环与低循环疲劳现象68
1 疲劳断裂破坏的理论基础68
第3章 疲劳断裂失效68
1.2 循环变形机制和力学描述69
1.3 疲劳裂纹的萌生与扩展理论72
1.4 疲劳短裂纹扩展理论74
1.5 非金属材料的疲劳77
2.1 接触疲劳失效:滑动、滚动、微动79
2 疲劳失效的类型79
2.2 腐蚀疲劳失效82
2.3 高温疲劳失效86
2.4 低温疲劳失效88
3.2 冷加工90
3.1 结构设计与材料90
3 疲劳失效的防治90
3.3 塑性加工91
3.4 喷丸处理93
3.5 热处理94
3.6 其他表面处理技术96
1.1 失效分析的基本方法与程序101
1 失效分析的方法101
第4章 机械零件的失效分析101
1.2 残骸分析法102
1.4 故障树分析法103
1.3 特征-因素图分析法103
2.1 常用实验检测技术的种类和选用原则105
2 失效分析的常用方法与技术105
1.5 失效模拟和加速失效模拟试验105
2.2 失效形态观测技术及其比较106
2.3 成分分析技术及其比较107
2.4 X射线分析技术及比较108
2.5 无损检测技术及其比较109
3.2 状态监测和控制112
3.1 失效补救112
3 失效的事后处理及预防112
3.4 剩余寿命预测113
3.3 断裂失效评定113
4.1 韧性断裂失效的判断114
4 典型失效的判断原则114
3.5 维修、更换及有关的维修技术114
4.2 脆性断裂失效的判断115
4.4 疲劳断裂的判断116
4.3 应力腐蚀断裂的判断116
4.5 磨损失效的判断118
参考文献119
第3篇 表面覆层形成与结合机理125
1.1 固体的表面127
1 表面与界面概述127
第1章 表面与覆层界面结合概述127
1.2 晶粒间界129
2.3 气相沉积膜层结合131
2.2 化学溶液沉积镀层结合131
2 覆层界面结合的类型131
2.1 覆层的冶金结合131
3.1 覆层界面的结合力132
3 覆层界面的结合性能与影响因素132
2.4 高分子涂层结合132
3.2 覆层界面结合性能的影响因素133
1.3 堆焊覆层的外延结晶134
1.2 堆焊覆层的冶金结合134
第2章 堆焊层的形成与结合134
1 覆层与基体的冶金结合134
1.1 堆焊概述134
2.1 覆层杂质的控制135
2 覆层成分的控制135
2.2 合金元素的控制137
3.1 熔合区的意义139
3 熔合区的特点139
3.2 熔合区的特征140
4.1 焊接热循环143
4 基材的受热变质143
4.2 基材变质问题144
5.1 焊接裂纹及控制146
5 焊接缺陷的控制146
5.2 气孔的形成及控制149
1.2 涂层的形成150
1.1 热喷涂的基本过程150
第3章 热熔融涂层的形成与结合150
1 热喷涂涂层的形成150
2.1 冶金结合151
2 热喷涂层与基材的结合形式151
3.2 孔隙152
3.1 润湿性152
2.2 机械嵌合152
2.3 物理-化学结合152
3 影响结合强度的主要因素152
4 提高涂层结合强度的措施153
3.4 基材表面状态153
3.3 氧化作用153
5.2 界面元素的互扩散154
5.1 涂层合金的润湿性及基材的适应性154
5 熔结结合的特点154
1.1 液相传质156
1 金属电沉积的反应步骤156
第4章 镀层的形成与结合156
1.4 相生成157
1.3 电化学步骤157
1.2 表面转化157
2.2 沉积物形态158
2.1 电结晶过程的动力学158
2 金属的电结晶过程158
3.2 镀层结合模式159
3.1 镀层结合的特点159
3 镀层的结合及其影响因素159
3.3 镀层结合的影响因素160
4 化学镀的特点161
1.2 化学吸附163
1.1 物理吸附163
第5章 气相沉积层的形成与结合163
1 气体与固体的相互作用163
2.2 单层生长型164
2.1 核生长型164
2 薄膜的生长164
3.3 非晶态薄膜的形成165
3.2 单晶薄膜的形成165
2.3 单层上的核生长165
3 不同晶态的形成165
3.1 多晶薄膜的形成165
4.3 离子镀的成膜及膜结构特点166
4.2 溅射镀膜的薄膜结构特点166
4 不同沉积方法的成膜及薄膜结构特点166
4.1 蒸发镀膜的薄膜结构特点166
4.4 离子束辅助沉积的成膜特点167
4.5 化学气相沉积的成膜特点168
5.2 影响薄膜附着力的因素169
5.1 不同界面的附着169
5 薄膜的附着力169
1.1 胶黏剂对被粘接表面的润湿性171
1 粘接的基本条件171
第6章 粘接层的形成与结合171
1.2 粘接力的形成172
2.2 扩散理论173
2.1 吸附理论173
2 粘接现象的各种理论解释173
3 粘涂层的成膜机理174
2.3 静电理论174
4.1 胶黏剂的组成及性质175
4 粘接强度的影响因素与控制175
4.2 被粘物表面状态176
4.5 工艺条件177
4.4 弱界面层177
4.3 粘接体系的内应力177
参考文献179
第4篇 涂装181
4 涂层质量评价183
3 涂覆设备183
第1章 概述183
1 涂覆材料的要求183
2 涂层组成183
1.2 涂料的配套原则185
1.1 涂料的选择185
第2章 涂装技术(材料)的选用原则185
1 涂料的配套选择原则185
2 涂装工艺和设备的选用原则186
3 涂装环境要求187
1.4 漆刷的维护188
1.3 刷涂注意事项188
第3章 通用涂装方法188
1 刷涂法188
1.1 基本原理188
1.2 刷涂工艺要求188
2.1 刮涂操作189
2 刮涂189
1.5 刷涂漆膜常见缺陷及改进189
2.3 刮涂腻子层常见缺陷及改进方法190
2.2 刮涂注意事项190
4.1 浸涂工艺191
4 浸涂191
3 滚刷191
3.1 滚刷的构造191
3.2 滚刷的种类191
3.3 滚刷涂操作191
5 淋涂192
4.3 浸涂漆膜常见缺陷及改进方法192
4.2 浸涂操作注意事项与设备维护192
7 压缩空气喷涂193
6 转鼓涂193
5.1 淋涂工艺与设备维护193
5.2 淋涂漆膜常见缺陷及改进方法193
7.2 空气喷涂作业194
7.1 空气喷涂的原理与特点194
方法195
7.3 喷涂作业注意事项、常见缺陷及改进195
7.5 喷枪的维护与故障处理197
7.4 喷枪的选择197
8 高压无气喷涂198
7.6 加热喷涂198
8.2 喷涂效率与喷涂工艺199
8.1 无气喷涂的原理与特点199
8.3 新型无气喷涂设备202
8.5 无气喷涂设备的选用与维护203
8.4 富锌涂料无气喷涂设备203
9.1 基本原理204
9 辊涂法204
9.2 辊涂工艺205
10.2 帘幕涂装工艺206
10.1 帘幕涂装机206
10 帘幕涂装法206
1.2 影响静电涂装的因素208
1.1 静电涂装的基本原理和特点208
第4章 特殊涂装方法208
1 静电涂装208
1.4 特种静电涂装210
1.3 静电涂装设备的选择原则210
2.2 电泳涂装的原理和特点211
2.1 概述211
2 电泳涂装211
2.4 影响电泳涂装的因素212
2.3 电泳涂装工艺过程212
2.5 电泳液参数测定214
2.7 电泳涂装漆膜常见疵病及防治方法215
2.6 电泳涂装废水处理215
3 粉末涂装216
3.1 粉末静电涂装法217
3.2 流化床涂装法219
3.3 静电流化床涂装法221
3.4 粉末电泳涂装法222
3.5 粉末涂料热熔射喷涂法223
2 防火224
1 防毒224
第5章 涂装中的安全与防护224
4 涂装安全生产措施225
3 防爆225
5.1 废气的治理226
5 “三废”治理226
5.2 废水处理227
参考文献228
第5篇 热喷涂229
3 热喷涂方法分类231
2 热喷涂技术特点231
第1章 概述231
1 热喷涂涂层形成原理231
4 涂层材料分类232
2 等离子电弧234
1 燃烧火焰特性234
第2章 热喷涂物理基础234
3.2 粒子的加速235
3.1 线材的雾化235
3 焰流与喷涂粒子动量传输特性235
4 焰流与喷涂粒子传热特性236
5.1 金属氧化的基础237
5 金属合金熔滴飞行过程中的氧化行为237
5.2 热喷涂金属粒子的氧化238
6.1 熔融粒子的扁平化239
6 喷涂粒子与基体的碰撞过程239
5.3 减少热喷涂金属粒子氧化的措施239
8 涂层内热应力的产生240
7 喷涂粒子在沉积涂层过程的时空独立性240
6.2 扁平粒子的冷却凝固240
9 涂层与基体的结合241
1.2 线材火焰喷涂设备242
1.1 线材火焰喷涂原理242
第3章 热喷涂方法与设备242
1 线材与棒材火焰喷涂242
2.2 粉末火焰喷涂设备243
2.1 粉末火焰喷涂原理243
1.3 线材火焰喷涂常用的喷涂材料243
1.4 线材火焰喷涂方法特点与应用243
1.5 棒材火焰喷涂方法特点与应用243
2 粉末火焰喷涂243
3 高速(超音速)火焰喷涂244
2.3 粉末火焰喷涂方法特点与应用244
3.3 燃气高速火焰喷涂245
3.2 高速火焰流的特征与系统构成245
3.1 高速(超音速)焰流产生条件245
3.6 高速火焰喷涂材料的发展现状246
3.5 典型高速火焰喷涂方法特征246
3.4 燃油高速火焰喷涂246
3.7 高速火焰喷涂涂层典型特征247
4.1 气体爆燃喷涂技术原理248
4 气体爆燃喷涂技术248
3.8 高速火焰喷涂方法的应用248
4.2 爆燃喷涂的若干气体动力学问题249
4.3 气体爆燃喷涂设备250
4.4 气体爆燃喷涂工艺参数选择251
4.5 气体爆燃喷涂材料及其应用253
5.2 电弧喷涂系统254
5.1 电弧喷涂原理254
5 电弧喷涂254
5.4 高速电弧喷涂技术255
5.3 电弧喷涂技术特点255
5.5 电弧喷涂材料256
5.6 高速电弧喷涂雾化特性257
5.7 高速电弧喷涂涂层特征258
5.8 高速电弧喷涂技术应用实例261
6.2 等离子喷涂系统的构成262
6.1 等离子喷涂原理262
6 等离子喷涂262
6.3 工作参数对等离子射流特性的影响263
7.2 高能水稳等离子喷涂265
7.1 超音速等离子喷涂265
6.4 等离子喷涂应用实例265
7 高能等离子喷涂265
9.2 冷喷涂方法原理266
9.1 冷喷涂技术的发展简介266
8 可控气氛与低气压等离子喷涂266
9 冷喷涂266
9.5 冷喷涂粒子沉积特性267
9.4 冷喷涂技术的特点267
9.3 冷喷涂系统的构成267
9.6 冷喷涂技术的应用268
2.1 普通线材269
2 线材材料种类与特征269
第4章 热喷涂材料与性能269
1 热喷涂材料分类269
3 粉末材料制备方法270
2.2 管状粉芯线材270
3.4 聚合制粉法271
3.3 烧结粉碎法271
3.1 雾化制粉法271
3.2 熔炼粉碎法271
6 氧化物陶瓷粉末272
5 高温合金粉末272
3.5 包覆制粉法272
4 自熔剂合金粉末与自粘结粉末272
4.1 自熔剂合金272
4.2 自粘结粉末272
6.2 氧化锆系陶瓷粉末273
6.1 氧化铝系陶瓷粉末273
7 金属陶瓷粉末274
6.4 氧化铬274
6.3 氧化钛274
2.4 超声清洗276
2.3 加热脱脂276
第5章 涂层制备工艺276
1 喷涂基体表面基本设计要求276
2 基体表面预处理——脱脂处理276
2.1 溶剂清洗276
2.2 碱液清洗276
3.1 喷砂处理277
3 基体表面粗化处理277
2.5 喷砂净化277
3.3 电拉毛278
3.2 机械加工法278
6.1 涂层的重熔处理279
6 涂层后热处理279
3.4 喷涂自黏结过渡层279
4 基体表面保护279
4.1 胶带保护279
4.2 化合物保护279
4.3 机械保护279
5 喷涂工艺选择原则279
7.2 封孔剂的选择280
7.1 封孔剂280
6.2 扩散处理280
7 封孔处理280
8.3 涂层砂带磨削和抛光281
8.2 涂层磨削加工281
8 表面加工281
8.1 机械加工281
2 涂层中的孔隙特征282
1 涂层急冷组织结构特征282
第6章 涂层组织结构与物理及力学性能282
4 涂层与基体的结合强度283
3 涂层的密度与孔隙率283
6.1 涂层的弹性模量284
6 涂层的弹性模量、强度与断裂韧度284
5 涂层的硬度与显微硬度284
7.1 涂层的摩擦与磨损285
7 涂层的摩擦与磨损特性285
6.2 涂层的强度285
6.3 涂层的断裂韧度285
6.4 典型涂层的弹性模量、强度与断裂韧度285
7.2 涂层的冲蚀磨损与涂层结构的关系286
9 涂层的介电特性287
8.2 比热容和辐射率287
7.3 涂层的耐磨性测定287
8 涂层的热物理性能287
8.1 热导率、热胀系数和热扩散率287
1 概述289
第7章 陶瓷与金属陶瓷涂层技术289
3 氧化钛涂层291
2 氧化铝涂层291
4 氧化锆涂层292
5 WC-Co系金属陶瓷涂层294
6 Cr3C2-NiCr金属陶瓷涂层296
2 塑料粉末涂料及其涂装技术应用及发展297
1 优质、高效、节能的环保型涂料297
第8章 塑料粉末热喷涂技术297
3.1 静电喷涂法298
3 塑料粉末涂料涂装技术298
3.4 分散液喷涂法299
3.3 静电流浸法299
3.2 流动浸塑法299
3.6 高能、高速塑料热喷涂技术300
3.5 粉末火焰喷涂法300
3.8 塑料涂覆层质量检验301
3.7 其他涂覆方法301
1.1 耐腐蚀涂层303
1 涂层性能303
第9章 涂层选用原则与应用303
1.5 绝缘或导电涂层304
1.4 耐高温热障涂层304
1.2 耐磨损涂层304
1.3 机械零件间隙控制涂层(可磨耗密封涂层)304
2 热喷涂层在航空航天领域的应用306
1.6 修补涂层306
3 热喷涂层在冶金领域的应用307
参考文献309
第6篇 堆焊311
2.1 堆焊金属的合金化及母材对堆焊金属的稀释313
2 堆焊的物理化学本质313
第1章 概述313
1 堆焊的特点及发展概况313
3.1 裂纹315
3 堆焊冶金缺陷315
2.2 堆焊层与母材的界面结合特点315
4.1 堆焊金属的耐磨性能316
4 堆焊金属的使用性能316
3.2 气孔316
4.2 堆焊金属的耐腐蚀性能317
4.5 堆焊金属的耐高温性能318
4.4 堆焊金属的耐气蚀性能318
4.3 堆焊金属的耐腐蚀磨损性能318
2 焊条电弧堆焊319
1.3 缺陷及其预防319
第2章 堆焊工艺方法及其特点319
1 氧乙炔火焰堆焊319
1.1 特点及其应用范围319
1.2 堆焊工艺319
3.1 特点及应用范围320
3 埋弧堆焊320
2.1 特点及应用范围320
2.2 堆焊工艺320
4 钨极氩弧堆焊321
3.2 堆焊工艺321
5.2 堆焊工艺322
5.1 特点及应用范围322
4.1 特点及应用范围322
4.2 堆焊工艺322
5 等离子弧堆焊322
6.1 MIG堆焊工艺及其应用323
6 熔化极气体保护堆焊323
6.4 振动堆焊工艺及其应用324
6.3 自保护电弧堆焊工艺及其应用324
6.2 CO2气体保护堆焊工艺及其应用324
7.1 特点325
7 电渣堆焊325
8 激光堆焊326
7.2 堆焊工艺326
9.1 聚焦光束粉末堆焊工艺327
9 聚焦光束粉末堆焊327
11.1 堆焊材料的形状328
11 堆焊方法的选择328
9.2 聚焦光束粉末堆焊应用328
10 摩擦堆焊328
11.5 经济性329
11.4 堆焊件的结构特点、冶金特点329
11.2 堆焊方法的特点329
11.3 堆焊层的性能要求329
1.1 铁基堆焊合金分类330
1 铁基堆焊合金330
第3章 堆焊合金及其应用330
1.2 铁基堆焊合金的堆焊工艺344
1.3 铁基堆焊合金的应用350
2.1 镍基堆焊合金分类351
2 镍基堆焊合金351
2.2 镍基堆焊合金的堆焊工艺353
3.1 钴基堆焊合金分类354
3 钴基堆焊合金354
2.3 镍基堆焊合金的应用354
3.2 钴基堆焊合金的堆焊工艺356
4.1 铜基堆焊合金分类及其应用357
4 铜基堆焊合金357
3.3 钴基堆焊合金的应用357
4.2 铜基堆焊合金的堆焊工艺359
5.1 复合堆焊合金的成分与牌号360
5 复合堆焊合金360
6.1 喷熔用自熔性合金粉末的成分与牌号362
6 自熔性合金粉末喷熔362
5.2 复合堆焊合金的应用362
5.3 复合堆焊合金的堆焊工艺362
7 堆焊合金的选择363
6.3 喷熔用自熔性合金粉末的喷熔工艺363
6.2 喷熔用自熔性合金粉末的应用363
2 阀门密封面堆焊367
1 轧辊堆焊367
第4章 典型零件的堆焊367
6 刮板输送机中部槽中板堆焊368
5 挖掘机铲斗和斗齿堆焊368
3 发动机关键部件的堆焊368
4 高炉料钟堆焊368
1.3 火焰堆焊369
1.2 高能束堆焊369
第5章 堆焊安全与防护369
1 堆焊过程中的有害因素369
1.1 电弧堆焊369
2.5 火焰堆焊回火防护措施370
2.4 高能束堆焊特殊防护措施370
2 安全防护措施370
2.1 通风防护措施370
2.2 个人防护措施370
2.3 放射性防护措施370
参考文献372
第7篇电镀与电刷镀373
1.1 电镀的应用和分类375
1 概述375
第1章 电镀375
1.2 电化学基本概念376
2.1 粗糙表面的整平380
2 表面预处理380
1.3 金属电沉积的基本理论380
2.2 脱脂382
2.3 浸蚀385
2.4 化学抛光和电化学抛光387
2.5 难镀金属的预处理388
3.2 氰化镀锌391
3.1 镀锌层的特性和用途391
3 电镀锌391
3.3 碱性锌酸盐镀锌393
3.4 氯化钾(钠)镀锌394
3.5 铵盐镀锌396
3.6 硫酸盐镀锌397
3.8 镀锌层钝化处理398
3.7 镀锌后除氢处理398
4.2 氰化物镀镉400
4.1 镀镉层的性质和用途400
4 电镀镉400
5.1 氰化物镀铜401
5 电镀铜401
4.3 氨羧络合物镀镉401
4.4 酸性镀镉401
4.5 镀后处理401
5.2 硫酸盐镀铜403
5.3 高分散能力光亮、半光亮硫酸盐镀铜405
5.5 其他无氰镀铜406
5.4 焦磷酸盐镀铜406
6.1 电镀瓦特镍和高氯化物镍(无添加剂)407
6 电镀镍407
6.2 镀镍添加剂408
6.3 电镀光亮镍410
6.4 电镀半光亮镍、高硫镍、镍封、高应力镍和多层镍411
6.6 电镀珍珠镍(缎面镍)414
6.5 电镀黑色镍和枪色镍414
7.1 电镀普通铬415
7 电镀铬415
6.7 电镀低应力镍415
7.2 稀土镀铬及电镀硬铬418
7.3 电镀黑铬419
7.4 三价铬镀铬420
8.1 电镀锡421
8 电镀锡和铁421
8.2 电镀铁425
9.1 电镀金427
9 电镀金、银及铂427
9.2 电镀银430
10.2 实现金属共沉积的措施433
10.1 金属共沉积的条件433
9.3 电镀铂433
10 合金电沉积概述433
10.4 金属共沉积的类型434
10.3 金属共沉积的特点和影响因素434
11.1 电镀锌镍合金435
11 电镀锌基合金435
10.5 合金镀层的分类435
11.2 电镀锌铁合金437
11.3 电镀锌钴合金438
11.4 电镀锡锌(锌锡)合金439
12.1 电镀铜锡合金440
12 电镀铜合金440
11.5 锌合金镀层的特性440
12.2 电镀铜锌合金442
12.3 电镀仿金层444
13.1 电镀镍铁合金445
13 电镀镍基合金445
13.2 电镀镍钴合金446
14.1 电镀锡铅和铅锡合金447
14 电镀锡基合金447
13.3 电镀镍磷合金447
14.3 电镀锡钴合金448
14.2 电镀锡镍合金448
15.2 电镀银锑合金449
15.1 电镀金基合金449
15 电镀金基合金和银锑合金449
16 复合电镀450
16.2 复合电镀的优缺点451
16.1 复合电镀的工艺特点451
16.4 复合镀层的类型和用途452
16.3 复合电镀机理452
16.5 复合电镀工艺453
16.6 典型复合电镀工艺举例455
17.2 非晶态合金电镀工艺456
17.1 非晶态合金镀层的类型和特点456
16.7 复合电镀的发展456
17 非晶态电镀456
17.4 非晶态镀层的特性和应用457
17.3 非晶态镀层的形成和沉积原理457
17.5 非晶态合金镀层的发展458
1 电刷镀技术发展概况459
第2章 电刷镀459
2.2 电刷镀技术特点462
2.1 电刷镀原理462
2 电刷镀原理及特点462
4.1 电刷镀镀液的分类463
4 电刷镀镀液463
3 电刷镀设备463
3.1 电刷镀电源设备463
3.2 电刷镀镀笔463
4.5 常用预处理溶液464
4.4 镀液选择原则464
4.2 电刷镀镀液的特点464
4.3 温度对镀液的pH值特性及导电性的影响464
4.6 常用电刷镀镀液466
5.2 电刷镀主要工艺参数的选择470
5.1 电刷镀的一般工艺过程470
5 电刷镀工艺470
5.4 镀层工艺规范的选择472
5.3 在不同金属材料上电刷镀472
5.5 工序间的水漂洗473
6.1 电刷镀层的结构474
6 电刷镀层的结构、结合机理与强化机理474
6.2 镀层与基体的结合机理475
6.3 镀层的强化机理476
7.2 定量检验477
7.1 定性检验477
6.4 镀层的再强化机理477
7 镀层质量检验477
8 电刷镀技术应用实例478
2.1 酸和碱480
2 有害物质的来源及危害性480
第3章 安全与防护480
1 有害物质浸入人体的途径480
1.1 经呼吸道浸入480
1.2 经皮肤浸入480
1.3 经消化道浸入480
3 电镀“三废”的产生及控制481
2.9 添加剂和表面活性剂等481
2.2 氰化物481
2.3 镉及镉化合物481
2.4 六价铬及三价铬481
2.5 铅及铅化合物481
2.6 镍及镍化合物481
2.7 铜及铜化合物481
2.8 氟化物481
4.2 采用低毒或无毒工艺482
4.1 全过程进行控制污染482
3.1 电镀产生的废液482
3.2 电镀产生的废气482
3.3 电镀产生的废渣482
4 电镀无害化生产的途径482
5 电镀工作人员操作注意事项483
4.6 加强管理483
4.3 采用逆流清洗技术483
4.4 低浓度工艺483
4.5 优化工艺483
参考文献485
第8篇 化学镀与转化膜技术487
2.1 化学镀镍的热力学489
2 化学镀镍机理489
第1章 概述489
1 化学镀的特点489
2.2 化学镀镍的动力学490
3 化学成膜处理分类491
5 化学转化膜的应用范围492
4 化学转化膜的防护性能492
3.1 按转化膜分类492
3.2 按金属种类分类492
3.3 按用途分类492
3.4 按施工方法分类492
1.2 还原剂493
1.1 主盐493
第2章 化学镀镍493
1 化学镀镍溶液的组成及其影响493
1.3 络合剂494
1.4 稳定剂497
1.6 缓冲剂及镀液的pH值498
1.5 加速剂498
2 化学镀镍溶液499
1.7 其他组份499
3.2 热学性质502
3.1 密度502
第3章 化学镀镍层的性能502
1 外观502
2 组织结构502
3 物理性质502
5 均镀能力503
4 力学性质503
3.3 电学性质503
3.4 磁学性质503
7 硬度与热处理504
6.4 热处理504
6 结合力及内应力504
6.1 基材504
6.2 前处理504
6.3 施镀工艺504
9 腐蚀行为505
8 钎焊性能505
9.4 孔隙率506
9.3 镀浴与耐蚀性506
9.1 电偶腐蚀506
9.2 镀层中磷含量及热处理与耐蚀性的关系506
9.5 化学镀镍层的腐蚀率507
10.1 黏着磨损512
10.2 磨料磨损512
10 磨损行为512
1.4 其他化学成分的浓度514
1.3 Na2HPO3·5H2O514
第4章 化学镀镍的质量控制及施镀工艺514
1 镀浴的监控514
1.1 Ni2+浓度514
1.2 还原剂浓度514
1.7 其他515
1.6 温度515
1.5 化学镀镍浴稳定性的测定515
2.4 孔隙率516
2.3 结合强度516
2 镀层质量的监控516
2.1 外观516
2.2 厚度516
2.6 内应力及硬度517
2.5 化学成分517
3.2 镀前处理518
3.1 镀浴518
2.7 耐磨性及耐蚀性518
3 化学镀镍故障及排除方法518
4.1 基材519
4 化学镀镍前处理519
3.3 机械设备519
3.4 镀浴污染519
3.5 排除故障的方法519
4.2 镀前处理须知521
4.4 铸铁件的镀前处理522
4.3 碳钢和低合金钢的前处理522
4.7 铝及铝合金的镀前处理523
4.6 铜及铜合金的镀前处理523
4.5 不锈钢、高合金钢的镀前处理523
4.9 钛及钛合金的镀前处理524
4.8 镁及镁合金的镀前处理524
4.10 其他金属及非金属材料的镀前处理525
5.2 提高镀层性能的后处理526
5.1 消除氢脆,提高结合力和硬度的镀后热处理526
5 化学镀层后处理526
6.1 钢铁件上镀层的退除527
6 化学镀镍层的退除527
6.5 镁及镁合金上镀层的退除528
6.4 铝及铝合金上镀层的退除528
6.2 不锈钢基体上镀层的退除528
6.3 铜及铜合金上镀层的退除528
2 汽车工业中的应用529
1 航空航天工业中的应用529
第5章 化学镀镍的工业应用及其设备529
3 化学工业中的应用530
7 军事工业中的应用531
6 采矿工业中的应用531
4 石油和天然气工业中的应用531
5 食品加工业中的应用531
9 其他工业中的应用532
8 电子和计算机工业中的应用532
10.1 镀槽533
10 化学镀镍设备533
10.3 供水和循环过滤534
10.2 加热器及搅拌装置534
1.1 化学镀铜溶液组成535
1 化学镀铜溶液535
第6章 化学镀铜535
3 化学镀铜层的性质及应用536
2 化学镀铜的操作和维护536
1.2 化学镀铜溶液536
1.2 化学镀银浴配方及工艺538
1.1 化学镀银浴组成及其反应机理538
第7章 化学镀贵金属538
1 镀银538
2.1 化学镀金浴的组成及其反应机理539
2 镀金539
1.3 化学镀银的注意事项539
2.2 化学镀金浴配方及工艺540
3.2 次磷酸盐浴542
3.1 肼浴542
3 镀钯542
4.1 肼浴543
4 镀铂543
4.2 硼氢化物浴544
1 化学镀钴545
第8章 化学镀钴及其合金545
2.3 Co-W-P及Co-Ni-W-P合金547
2.2 Co-Fe-P合金配方547
2 化学镀钴基多元合金膜547
2.1 Co-Ni-P合金547
2.6 Co-Fe-B合金548
2.5 其他Co-Me(Cu、Mo、Re)-P合金548
2.4 Co-Zn-P合金548
1.2 Ni-Fe-P549
1.1 Ni-Co-P549
第9章 化学镀镍基多元合金549
1 Ni-Me-P系三元合金549
1.4 Ni-W-P550
1.3 Ni-Cu-P550
1.5 Ni-Mo-P551
2 Ni-Me-B系三元合金552
1.9 Ni-Zn-P552
1.6 Ni-Sn-P552
1.7 Ni-Re-P552
1.8 Ni-Cr-P552
2.4 Ni-Me(Mo、W、Zn、Re)-B553
2.3 Ni-Sn-B553
2.1 Ni-Co-B553
2.2 Ni-Fe-B553
2.5 Ni-P-B554
1.1 Ni-P/SiC555
1 耐磨镀层555
第10章 化学复合镀555
1.3 其他化学复合镀耐磨镀层556
1.2 Ni-P(B)/金刚石556
2 自润滑镀层557
1.1 阳极氧化膜的生成机理及其性质559
1 铝和铝合金的阳极氧化559
第11章 电化学转化膜559
1.2 铝合金阳极氧化方法560
2.1 镁合金的阳极氧化567
2 其他金属的阳极氧化567
2.2 铜和铜合金的阳极氧化568
2.4 钢的阳极氧化569
2.3 硅、锗、钽、锆、钛、锌和镉的阳极氧化569
1.1 钢铁的化学氧化(钢铁发蓝)570
1 化学氧化法570
第12章 化学转化膜570
1.2 钢铁化学发黑新工艺571
1.3 铝和铝合金的化学氧化572
2.2 磷化膜的性质574
2.1 磷化膜形成的基本原理574
1.4 铜和铜合金的化学氧化574
2 磷酸盐处理574
2.3 各种金属的磷酸盐处理575
4 锌、镉、铜及其他有色金属的铬酸盐处理579
3 钢铁的草酸盐处理579
4.2 膜的基本性质580
4.1 基本原理580
1.1 自然发色法582
1 铝和铝合金阳极氧化着色处理582
第13章 金属着色技术582
1.2 电解着色法583
1.3 吸附染色法(化学染色法)584
2.2 铜和黄铜着色工艺588
2.1 着色前处理588
2 铜和黄铜层的着色588
4.1 锌层着色589
4 锌层的着色和染色589
3 镍层的着色和染色589
3.1 镍层的着色589
3.2 镍层的染色589
5.1 不锈钢氧化着色法原理590
5 不锈钢着色590
4.2 锌层染色590
5.2 不锈钢着色举例591
1.1 铝和铝合金的阳极氧化膜的检验592
1 转化膜的检验592
第14章 转化膜工艺质量控制592
1.2 磷酸盐膜的检验593
2.1 铝和铝合金阳极氧化电解液的分析594
2 转化膜处理液的检测594
1.3 铬酸盐膜的检验594
2.2 磷酸盐处理液的检验及试验方法596
2.4 铬酸盐处理液的分析598
2.3 草酸盐处理液的分析598
3.3 铬酸盐膜标准599
3.2 磷酸盐膜标准599
3 转化膜标准规范599
3.1 铝氧化膜标准599
参考文献600
第9篇 化学热处理601
第1章 概述603
3.1 扩散过程的宏观规律605
3 吸收原子在金属中的扩散605
第2章 化学热处理原理605
1 渗剂中的物理化学过程605
1.1 渗剂中的化学反应605
1.2 催化剂的作用605
2 化学热处理中的相界面反应605
4 提高化学热处理速度的方法606
3.2 反应扩散和渗层的显微组织606
4.3 采用催渗办法607
4.2 优化工艺607
4.1 适当提高工艺温度607
2.1 气体渗碳气氛608
2 气体渗碳608
第3章 钢的渗碳608
1 渗碳的基本工艺参数608
1.1 渗碳温度608
1.2 渗碳时间608
1.3 碳势及其控制608
2.3 炉气碳势的测量与控制610
2.2 气体渗碳过程中的化学反应610
3 其他渗碳方法612
2.4 气体渗碳工艺612
4.2 渗碳后热处理613
4.1 渗碳用钢613
3.1 固体渗碳工艺613
3.2 液体渗碳613
3.3 流化床渗碳613
3.4 离子渗碳613
3.5 真空渗碳613
4 渗碳用钢及渗碳后热处理613
6.1 渗碳件质量检验614
6 渗碳件质量检测及常见缺陷的防止措施614
5 渗碳层的组织和性能614
5.1 渗碳层的组织特点614
5.2 渗碳后钢的性能614
7.2 乙炔低压渗碳615
7.1 高温渗碳615
6.2 渗碳件常见缺陷及防止措施615
7 渗碳技术的发展与展望615
1.1 气体碳氮共渗原理617
1 气 体碳氮共渗617
第4章 钢的碳氮共渗617
3 碳氮共渗用钢及共渗后的热处理618
2 液体碳氮共渗及其他方法618
1.2 碳氮共渗介质及其控制618
1.3 共渗温度与时间618
6 碳氮共渗应用实例619
5.2 不正常碳氮化合物619
4 共渗层的组织和性能619
5 碳氮共渗层常见缺陷与预防方法619
5.1 黑色组织619
7 碳氮共渗技术的发展620
1.3 渗氮强化机制621
1.2 渗氮层的形成621
第5章 钢的渗氮621
1 渗氮原理621
1.1 Fe-N系中的相组成621
1.4 常用渗氮钢622
2.1 渗氮反应及气氛控制623
2 气体渗氮623
1.5 渗氮用钢的预先处理623
3.2 固体渗氮624
3.1 盐浴渗氮624
2.2 渗氮工艺参数及控制624
2.3 影响渗氮层硬度的主要因素624
3 其他渗氮方法624
5.1 工艺625
5 渗氮与渗碳的比较625
4 渗氮零件的检验和缺陷625
4.1 质量检验625
4.2 渗氮缺陷及预防625
6.1 可控渗氮626
6 渗氮技术的发展与展望626
5.2 性能626
5.3 成本626
6.2 离子渗氮627
1.1 盐浴氮碳共渗628
1 铁素体氮碳共渗628
第6章 氮碳共渗628
1.2 气体氮碳共渗629
2.2 组织与性能631
2.1 原理及工艺631
1.3 铁素体氮碳共渗层的组织与性能631
1.4 其他氮碳共渗技术631
1.5 应用实例-替代气体渗氮631
2 奥氏体氮碳共渗631
3 氮碳共渗后氧化处理632
2.4 工业应用实例632
2.3 工艺发展632
3.3 其他处理方法633
3.2 气态处理633
3.1 液态处理633
1.3 渗硼工艺方法634
1.2 渗硼层组织特征634
第7章 渗硼和渗硫634
1 钢的渗硼634
1.1 渗硼的特点与应用634
1.5 合金元素的影响635
1.4 渗硼后的处理635
2.2 硼-金属共渗与复合渗636
2.1 硼-碳复合渗636
1.6 适合渗硼的金属材料636
1.7 渗硼层的性能636
2 含硼共渗与复合渗636
3.2 含硫共渗637
3.1 钢的渗硫637
3 渗硫及含硫共渗637
2.1 渗铝工艺方法639
2 钢的渗铝639
第8章 渗金属639
1 渗金属原理与工艺分类639
1.1 镀-渗法639
1.2 扩散型渗金属639
1.3 热反应沉积渗金属639
2.3 渗铝的应用640
2.2 渗铝层组织与性能特点640
3.2 渗铬层组织641
3.1 渗铬工艺641
3 钢铁渗铬641
4.2 硼砂碳化物覆层工艺642
4.1 硼砂碳化物覆层法原理642
3.3 渗铬层性能与应用642
4 碳化物覆层工艺642
5.2 镀-渗锡青铜643
5.1 镀-渗锡643
4.3 渗层性能与应用643
5 镀渗锡及铜锡合金643
6.4 离子渗金属应用644
6.3 多弧离子渗金属644
6 渗金属技术的发展——离子渗金属644
6.1 气相辉光离子渗金属644
6.2 双层辉光离子渗金属644
2.1 离子渗氮的原理645
2 离子渗氮645
第9章 等离子化学热处理645
1 等离子体及其产生645
2.3 离子渗氮的工艺参数646
2.2 离子渗氮钢的组织646
2.5 离子渗氮技术新进展647
2.4 离子渗氮的特点647
3.2 气体成分对化合物层组织结构的影响649
3.1 离子氮碳共渗的特点649
3 离子氮碳共渗649
4.2 离子渗碳层的组织和性能650
4.1 离子渗碳的原理及设备650
3.3 冷却速度对化合物层组织结构的影响650
4 离子渗碳650
4.3 离子渗碳的特点651
1.1 渗氮处理652
1 钛合金化学热处理652
第10章 有色金属和不锈钢的化学热处理652
1.2 渗氧处理653
1.4 渗硅和渗铝654
1.3 渗碳和渗硼654
2.1 镀-渗工艺655
2 铝合金的化学热处理655
1.5 渗镍和渗铜655
3 奥氏体不锈钢的等离子低温表面合金化656
2.2 等离子渗氮656
3.3 S相的性能657
3.2 S相的组织657
3.1 S相的形成条件657
3.5 应用658
3.4 S相的热稳定性658
参考文献659